A Simple Preparation Method of Phenolic Resin Microspheres Without Dispersant
A technology of phenolic resin and dispersing agent, which is applied in the field of simple preparation of phenolic resin microspheres, can solve the problems of inability to form spheres and the like, and achieve the effects of reducing raw material cost, good reproducibility and cost reduction.
- Summary
- Abstract
- Description
- Claims
- Application Information
AI Technical Summary
Problems solved by technology
Method used
Examples
Embodiment 1
[0017] Add 0.5 times the mass of ethanol solvent to the commercially purchased thermosetting phenolic resin, stir briefly to obtain a slurry, and then directly add the slurry to heat transfer oil and silicone oil at a temperature of 70°C with a volume ratio of 1:8 , start stirring, control the stirring rate to 150 rpm, then keep the temperature for 2 hours, separate solid and liquid, wash and dry to obtain phenolic resin microspheres.
[0018] The diameter of the phenolic resin microspheres is between 80-100 microns, and the sphericity is greater than 95%.
Embodiment 2
[0020] Add 4 times the mass of methanol solvent to commercially purchased thermoplastic phenolic resin, stir briefly to obtain a slurry, and then directly add the slurry to heat transfer oil and silicone oil at a temperature of 100°C with a volume ratio of 1:4 , start stirring, control the stirring rate to 250 rpm, then keep the temperature for 0.5h, separate solid and liquid, wash and dry to obtain phenolic resin microspheres.
[0021] The diameter of the phenolic resin microspheres is between 20-30 microns, and the sphericity is greater than 98%.
Embodiment 3
[0023] Add 1 times the mass of ethanol solvent to the commercially purchased thermosetting phenolic resin, stir briefly to obtain a slurry, and then directly add the slurry to heat transfer oil and silicone oil at a temperature of 85°C with a volume ratio of 1:1 , start stirring, control the stirring rate to 300 rpm, then keep the temperature for 1 hour, separate solid and liquid, wash and dry to obtain phenolic resin microspheres.
[0024] The diameter of the phenolic resin microspheres is between 50-90 microns, and the sphericity is greater than 91%.
PUM
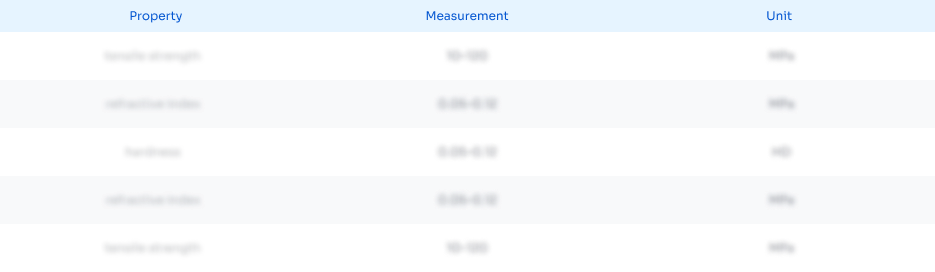
Abstract
Description
Claims
Application Information

- R&D Engineer
- R&D Manager
- IP Professional
- Industry Leading Data Capabilities
- Powerful AI technology
- Patent DNA Extraction
Browse by: Latest US Patents, China's latest patents, Technical Efficacy Thesaurus, Application Domain, Technology Topic, Popular Technical Reports.
© 2024 PatSnap. All rights reserved.Legal|Privacy policy|Modern Slavery Act Transparency Statement|Sitemap|About US| Contact US: help@patsnap.com