Magnetic core forming device and forming process for laser printer
A laser printer and forming device technology, applied in the manufacture of inductors/transformers/magnets, electrical components, circuits, etc., can solve the problems of long injection molding time and cooling time, low actual production capacity, easy deformation and bending, etc., and achieve stable product quality , The overall consistency of the product is good, and the production cost is low
- Summary
- Abstract
- Description
- Claims
- Application Information
AI Technical Summary
Problems solved by technology
Method used
Image
Examples
Embodiment Construction
[0026] In order to make the technical means, creative features, goals and effects achieved by the present invention easy to understand, the present invention will be further described below in conjunction with specific embodiments.
[0027] refer to Figure 1-2 , the specific embodiment adopts the following technical solutions: a laser printer magnetic core forming device, including an extruder barrel 1, an extrusion screw 2, a machine head 3, an evacuated core 4, a shaping device 5, an electromagnetic orientation device 6, Cooling device 7, cooling water channel 8, traction device 9 and cutting device 10, extruder barrel 1 is connected to the front end of machine head 3, extrusion screw 2 is arranged in the center of extruder barrel 1, and rear end of machine head 3 is arranged in sequence There are a shaping device 5, a cooling device 7, a traction device 9 and a cutting device 10, the shaping device 5 is provided with an electromagnetic orientation device 6, the cooling dev...
PUM
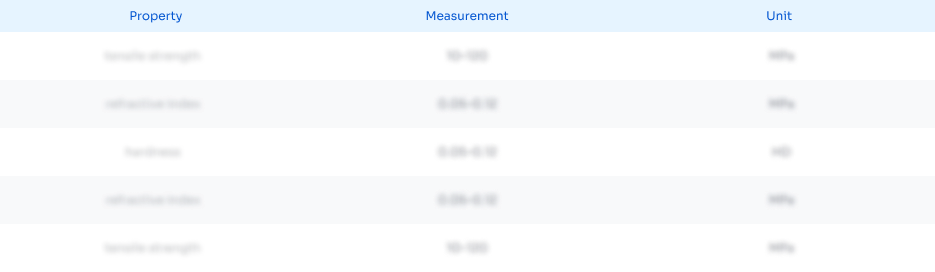
Abstract
Description
Claims
Application Information

- Generate Ideas
- Intellectual Property
- Life Sciences
- Materials
- Tech Scout
- Unparalleled Data Quality
- Higher Quality Content
- 60% Fewer Hallucinations
Browse by: Latest US Patents, China's latest patents, Technical Efficacy Thesaurus, Application Domain, Technology Topic, Popular Technical Reports.
© 2025 PatSnap. All rights reserved.Legal|Privacy policy|Modern Slavery Act Transparency Statement|Sitemap|About US| Contact US: help@patsnap.com