Force deformation error calculation method for pin roller linear guide rail pair under vertical loads
A roller linear guide, vertical load technology, used in computing, special data processing applications, instruments, etc.
- Summary
- Abstract
- Description
- Claims
- Application Information
AI Technical Summary
Problems solved by technology
Method used
Image
Examples
Embodiment Construction
[0059] The present invention takes the four-slider workbench roller linear guide pair as the research object, calculates the force deformation error under the action of vertical load, and verifies the practicability of the present invention.
[0060] Step 1: Establish a three-dimensional model and calculate the external force on the roller linear guide pair.
[0061] Taking the sub-center of the base guide rail as the origin of coordinates, establish a 3D model of the upper body of the machine tool, such as Figure 5 shown. Set the material of the parts, the material of the guide rail and the slider is GCr15, isotropic, the medium is uniform, and the density of the material is 7800kg / m 3 ;The material of the main parts such as columns and beams is HT200, and the density is 7200kg / m 3 .
[0062] Using the quality attributes, the mass M of the upper body of the machine tool is obtained as 1731.41kg; then the gravity G of the upper body of the machine tool borne by the guide r...
PUM
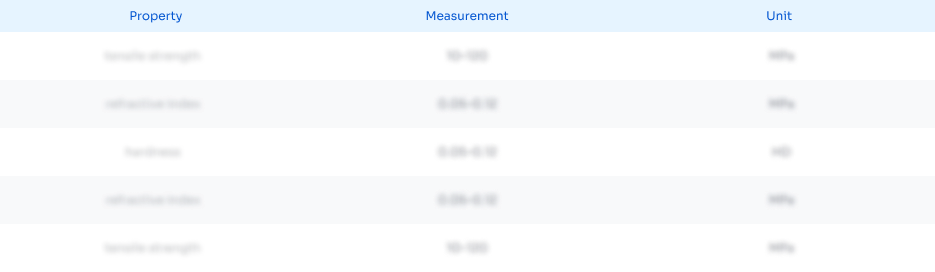
Abstract
Description
Claims
Application Information

- Generate Ideas
- Intellectual Property
- Life Sciences
- Materials
- Tech Scout
- Unparalleled Data Quality
- Higher Quality Content
- 60% Fewer Hallucinations
Browse by: Latest US Patents, China's latest patents, Technical Efficacy Thesaurus, Application Domain, Technology Topic, Popular Technical Reports.
© 2025 PatSnap. All rights reserved.Legal|Privacy policy|Modern Slavery Act Transparency Statement|Sitemap|About US| Contact US: help@patsnap.com