Method for reducing three-shaft linkage contour error
A contour error and three-axis linkage technology, which is applied in the direction of instruments, computer control, simulators, etc., can solve the problems of the difficulty in implementing highly integrated CNC machine tools and the inability to reduce multi-axis linkage contour errors, etc.
- Summary
- Abstract
- Description
- Claims
- Application Information
AI Technical Summary
Problems solved by technology
Method used
Image
Examples
Embodiment Construction
[0047] The specific implementation manner of the present invention will be described in detail in conjunction with the technical scheme and the accompanying drawings.
[0048] When using high feed speed to process complex curved surface parts, due to the existence of variable curvature tool rails, the dynamic characteristics of CNC machine tools, the mechanical inertia of the processing feed axis and other factors, there will be a large follow-up error and the actual processing feed speed is very easy to reach The phenomenon that the speed value is less than the command speed value will induce multi-axis linkage contour error, which is not conducive to the precise and efficient machining of complex curved surface parts with variable curvature. Accordingly, aiming at the multi-axis linkage contour error in high feed rate machining, a method to reduce the three-axis linkage contour error was invented.
[0049] Taking the space star line tool path represented by non-uniform ratio...
PUM
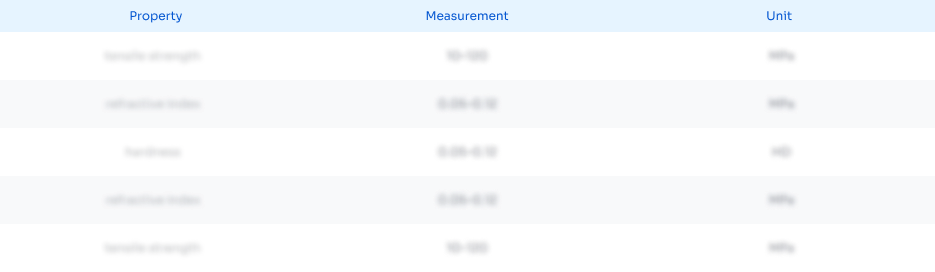
Abstract
Description
Claims
Application Information

- R&D
- Intellectual Property
- Life Sciences
- Materials
- Tech Scout
- Unparalleled Data Quality
- Higher Quality Content
- 60% Fewer Hallucinations
Browse by: Latest US Patents, China's latest patents, Technical Efficacy Thesaurus, Application Domain, Technology Topic, Popular Technical Reports.
© 2025 PatSnap. All rights reserved.Legal|Privacy policy|Modern Slavery Act Transparency Statement|Sitemap|About US| Contact US: help@patsnap.com