Tower drum doorframe gradually varied in thickness
A gradual change type and door frame technology, which is applied in the direction of wind turbine components, wind engines, mechanical equipment, etc., can solve the problems of increased welding heat and welding deformation, increasing the difficulty of welding deformation control, and increasing the difficulty of tower 1 hoisting, etc., to achieve The effect of reducing stress concentration, reducing transportation difficulty, and high fatigue resistance
- Summary
- Abstract
- Description
- Claims
- Application Information
AI Technical Summary
Problems solved by technology
Method used
Image
Examples
Embodiment 1
[0023] Embodiment 1: as Figure 5-Figure 7 As shown, the present invention comprises door frame upper end 13, door frame middle part 14 and door frame lower end 15 and smooth transition between door frame upper end 13, door frame lower end 15 and door frame middle part 14; The inner wall of the tower tube 1 adopts a smooth transition, and the thickness of the inner wall 20 of the door frame is thicker than that of the outer wall 19 of the door frame.
[0024] by Figure 1-Figure 4 Take an 80m high wind power tower project as an example. If no door opening is provided, the wall thickness of the bottom tower can be 28mm, the total weight of the bottom tower is 59.3 tons, and the total weight of the wind power tower body is 194.1 tons. The second-order natural frequency is 0.86288Hz; if a door opening is opened and a ring-stiffened door frame 6 is used to strengthen the opening, the wall thickness of the bottom tower needs to be increased to 37mm, and the connection between the ...
PUM
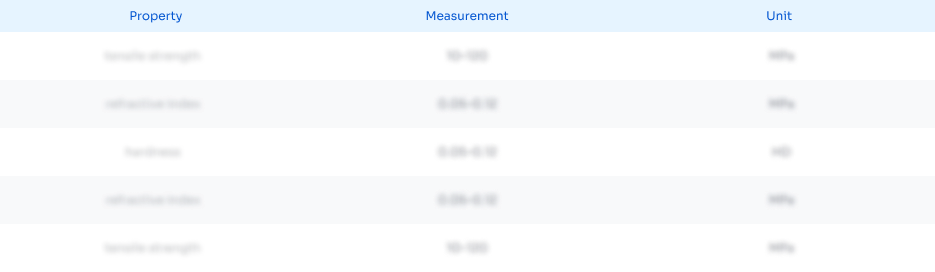
Abstract
Description
Claims
Application Information

- Generate Ideas
- Intellectual Property
- Life Sciences
- Materials
- Tech Scout
- Unparalleled Data Quality
- Higher Quality Content
- 60% Fewer Hallucinations
Browse by: Latest US Patents, China's latest patents, Technical Efficacy Thesaurus, Application Domain, Technology Topic, Popular Technical Reports.
© 2025 PatSnap. All rights reserved.Legal|Privacy policy|Modern Slavery Act Transparency Statement|Sitemap|About US| Contact US: help@patsnap.com