U-type vibration isolating device with novel composite material structure
A composite material, vibration isolation technology, applied in the direction of propulsion engine, transportation and packaging, ship construction, etc., to achieve the effect of light weight, high bending stiffness and convenient molding
- Summary
- Abstract
- Description
- Claims
- Application Information
AI Technical Summary
Problems solved by technology
Method used
Image
Examples
Embodiment Construction
[0024] The specific implementation manner of the present invention will be described below in conjunction with the accompanying drawings.
[0025] Such as figure 1 As shown, a U-shaped vibration isolation device with a new composite material structure includes an equipment installation base 4, and the equipment installation base 4 is fixedly connected to a sandwich composite vibration isolation raft 1, and the sandwich composite vibration isolation raft 1 is at least It consists of two sandwich composite material structural beams 101 arranged at intervals. In the present invention, there are two sandwich composite material structural beams 101, which are located on the inside and outside of each sandwich composite material structural beam 101, and between the sandwich composite material structural beams 101. The end of the hull is connected to the hull steel base 3 through the vibration isolator 2. The hull steel base 3 is composed of the first layer panel 31, the second layer...
PUM
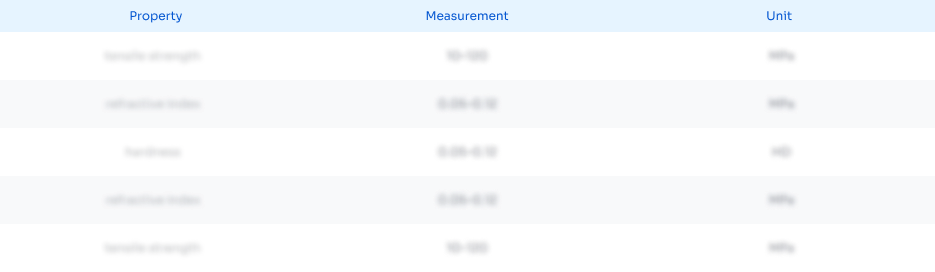
Abstract
Description
Claims
Application Information

- R&D Engineer
- R&D Manager
- IP Professional
- Industry Leading Data Capabilities
- Powerful AI technology
- Patent DNA Extraction
Browse by: Latest US Patents, China's latest patents, Technical Efficacy Thesaurus, Application Domain, Technology Topic, Popular Technical Reports.
© 2024 PatSnap. All rights reserved.Legal|Privacy policy|Modern Slavery Act Transparency Statement|Sitemap|About US| Contact US: help@patsnap.com