A two-degree-of-freedom eddy current tuned passive damper
A passive damping and eddy current technology, applied in the direction of springs/shock absorbers, maintenance and safety accessories, mechanical equipment, etc., can solve the problems of vibration energy dissipation, narrow suppression frequency band, damage and failure of eddy current dampers, etc. Vibration frequency bandwidth, good thermal conductivity, and good vibration suppression effect
- Summary
- Abstract
- Description
- Claims
- Application Information
AI Technical Summary
Problems solved by technology
Method used
Image
Examples
Embodiment Construction
[0030] specific implementation plan
[0031] The present invention will be further described in detail below in conjunction with the accompanying drawings.
[0032] The present invention is a two-degree-of-freedom electric eddy current tuned passive damper, such as figure 1 , figure 2 , image 3 , Figure 4 As shown, it includes a mass block 1, a support frame 2, a cylindrical rod 3, a stiffness adjusting nut 4, a permanent magnet 5, and a support plate 6.
[0033] The relationship between them is: the cylindrical rod passes through the mass block, and is connected with the mass block through threads; the cylindrical rod and the support frame are in clearance fit, and are tightened and positioned by the stiffness adjustment nuts on both sides of the support frame; the bottom of the four support frames are located on the same Plane; the permanent magnet is fixed on the support plate, and the support plate is pasted on the workpiece, and the position of the support plate is...
PUM
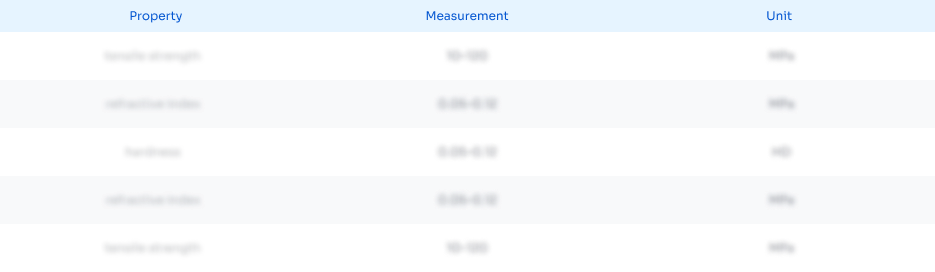
Abstract
Description
Claims
Application Information

- R&D
- Intellectual Property
- Life Sciences
- Materials
- Tech Scout
- Unparalleled Data Quality
- Higher Quality Content
- 60% Fewer Hallucinations
Browse by: Latest US Patents, China's latest patents, Technical Efficacy Thesaurus, Application Domain, Technology Topic, Popular Technical Reports.
© 2025 PatSnap. All rights reserved.Legal|Privacy policy|Modern Slavery Act Transparency Statement|Sitemap|About US| Contact US: help@patsnap.com