Multi-degree-of-freedom bionic joint
A technology of bionic joints and degrees of freedom, applied in the field of bionic joints, can solve problems such as difficult to move flexibly, increase the difficulty of load and structural design, and lengthen, so as to achieve flexible and light structural composition, shorten the energy transmission chain, and simple structural composition Effect
- Summary
- Abstract
- Description
- Claims
- Application Information
AI Technical Summary
Problems solved by technology
Method used
Image
Examples
Embodiment Construction
[0015] The present invention will be further described in detail below in conjunction with the accompanying drawings and specific embodiments.
[0016] to combine Figure 1 to Figure 5 , the present invention includes a moving part 1, a supporting part 2 and a driving part 3, the upper end of the supporting part 2 is a concave articular surface 23, the side end is provided with a convex joint 22, the lower end of the moving part 1 is a spherical body 12, and the The spherical body 12 is fitly installed in the concave articular surface 23, and the driving part 3 includes a flexible wire 33 connecting the spherical body 12 and the concave articular surface 23, and two groups of rotating muscles connecting the convex joint 22 and the moving part 1 Units 35, 36 and four groups of stretching muscle units 34 are symmetrically arranged between the upper edge of the supporting part 2 and the moving part 1, and the two groups of rotating muscle units 35, 36 are symmetrically arranged o...
PUM
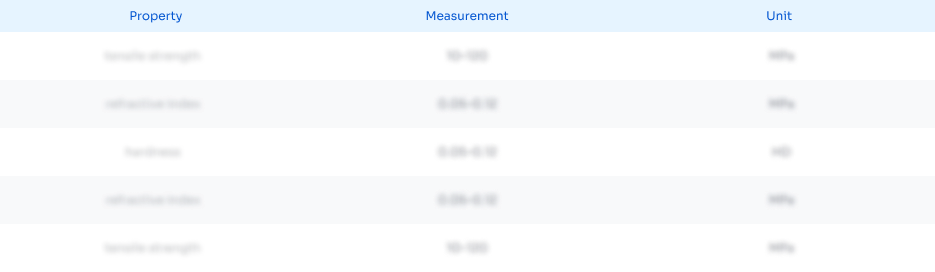
Abstract
Description
Claims
Application Information

- R&D Engineer
- R&D Manager
- IP Professional
- Industry Leading Data Capabilities
- Powerful AI technology
- Patent DNA Extraction
Browse by: Latest US Patents, China's latest patents, Technical Efficacy Thesaurus, Application Domain, Technology Topic, Popular Technical Reports.
© 2024 PatSnap. All rights reserved.Legal|Privacy policy|Modern Slavery Act Transparency Statement|Sitemap|About US| Contact US: help@patsnap.com