Fumaric acid diester-cinnamic acid ester copolymer, method for producing same, and film using same
A technology of fumaric acid diester and cinnamic acid esters, which is applied in the direction of coating, etc., can solve the problems of low heat resistance, small phase difference, and insufficient properties of the phase difference film, and achieve the effect of excellent characteristics and high-efficiency manufacturing
- Summary
- Abstract
- Description
- Claims
- Application Information
AI Technical Summary
Problems solved by technology
Method used
Examples
Embodiment 1
[0055] Example 1 (production of diisopropyl fumarate-ethyl cinnamate copolymer)
[0056] Put 50 g (0.25 mol (95.02 mol%)) of diisopropyl fumarate and 2.3 g (0.013 mol (4.94 mol%)) of ethyl cinnamate into a glass ampoule with a capacity of 75 mL. Monomer divinylbenzene 0.014g (1.1×10 -4 mol (0.04 mol %)) and 0.29 g (0.0016 mol (0.61 mol %)) of tert-butyl peroxypivalate as a polymerization initiator, after performing nitrogen substitution and depressurization, they were sealed under reduced pressure. Radical polymerization was performed by placing this ampoule in a thermostat at 50° C. and maintaining it for 144 hours. After the polymerization reaction was completed, the polymer was taken out from the ampoule and dissolved in 400 g of tetrahydrofuran. After dropping this polymer solution into 3 L of methanol to precipitate it, vacuum-dry it at 80° C. for 10 hours to obtain 28.8 g of diisopropyl fumarate-ethyl cinnamate copolymer (yield: 55%).
[0057] The number average molecu...
Embodiment 2
[0059] Example 2 (production of diisopropyl fumarate-ethyl cinnamate copolymer)
[0060] Put 50 g (0.25 mol (85.24 mol%)) of diisopropyl fumarate and 7.6 g (0.043 mol (14.66 mol%)) of ethyl cinnamate into a glass ampoule with a capacity of 75 mL. Monomer divinylbenzene 0.038g (2.9×10 -4 mol (0.10 mol%)) and 0.32 g (0.0018 mol (0.61 mol%)) of tert-butyl peroxypivalate as a polymerization initiator were repeatedly subjected to nitrogen substitution and decompression, and then sealed under reduced pressure. Radical polymerization was performed by placing this ampoule in a thermostat at 50° C. and maintaining it for 144 hours. After the polymerization reaction was completed, the polymer was taken out from the ampoule and dissolved in 400 g of tetrahydrofuran. After dropping this polymer solution into 3 L of methanol to precipitate it, vacuum-dry it at 80° C. for 10 hours to obtain 32.3 g of diisopropyl fumarate-ethyl cinnamate copolymer (yield: 57%).
[0061] The number averag...
Embodiment 3
[0063] Example 3 (production of diisopropyl fumarate-ethyl cinnamate copolymer)
[0064] 50 g (0.25 mol (69.99 mol %)) of diisopropyl fumarate, 18.9 g (0.107 mol (29.96 mol %)) of ethyl cinnamate, as radical polymerizable polyfunctional 0.064g (1.8×10 -4 mol (0.05 mol %)) and 0.39 g (0.0023 mol (0.64 mol %)) of tert-butyl peroxypivalate as a polymerization initiator were repeatedly subjected to nitrogen substitution and decompression, and then sealed under reduced pressure. Radical polymerization was performed by placing this ampoule in a thermostat at 50° C. and maintaining it for 168 hours. After the polymerization reaction was completed, the polymer was taken out from the ampoule and dissolved in 400 g of tetrahydrofuran. The polymer solution was dropped into 3 L of methanol to precipitate it, and then vacuum-dried at 80° C. for 10 hours to obtain 35.2 g of diisopropyl fumarate-ethyl cinnamate copolymer (yield: 51%).
[0065] The number average molecular weight of the o...
PUM
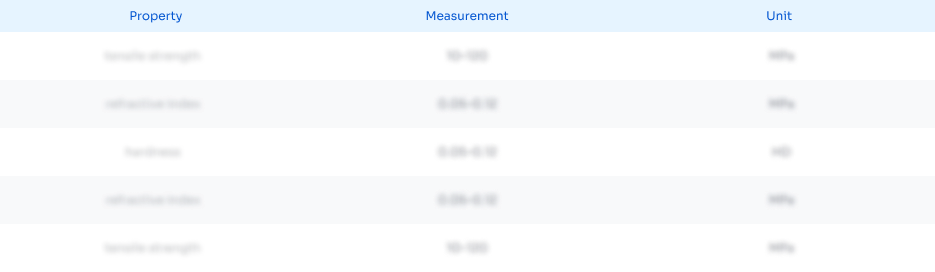
Abstract
Description
Claims
Application Information

- Generate Ideas
- Intellectual Property
- Life Sciences
- Materials
- Tech Scout
- Unparalleled Data Quality
- Higher Quality Content
- 60% Fewer Hallucinations
Browse by: Latest US Patents, China's latest patents, Technical Efficacy Thesaurus, Application Domain, Technology Topic, Popular Technical Reports.
© 2025 PatSnap. All rights reserved.Legal|Privacy policy|Modern Slavery Act Transparency Statement|Sitemap|About US| Contact US: help@patsnap.com