Inner rotor cooling type high-power eddy speed regulator
An inner rotor, high-power technology, applied in the field of inner-rotor cooling high-power eddy current governor, can solve the problems of cooling medium infiltration, lubrication system equipment failure, increased processing difficulty, etc., to facilitate assembly and maintenance, large Power eddy current speed regulation, realize the effect of eddy current speed regulation
- Summary
- Abstract
- Description
- Claims
- Application Information
AI Technical Summary
Problems solved by technology
Method used
Image
Examples
Embodiment 1
[0045] Such as figure 1 As shown, a high-power vortex speed governor with inner rotor cooling includes an inner rotor, an outer rotor coaxially arranged with the inner rotor, and a coolant supply and discharge system.
[0046] The inner rotor includes an inner rotor shaft 3 , an inner rotor rotating disc 9 and two conductive metal discs 91 .
[0047] A first sealed cavity 92 is provided inside the inner rotor shaft 3 along the axial direction.
[0048] The inner rotor rotating disk 9 is coaxially and fixedly sleeved on the outer periphery of the left end of the inner rotor shaft 3 , and the inner rotor rotating disk 9 is provided with a second sealed cavity 93 along the radial direction. Preferably, the inner rotor rotating disk 9 and the inner rotor shaft 3 are integrally arranged.
[0049] Two conductive metal discs 91 are respectively coaxially fixed on both sides of the inner rotor rotating disc 9, such as Figure 8 As shown, each side of the inner rotor rotating di...
Embodiment 2
[0095] The structure and principle of embodiment 2 are basically the same as embodiment 1, the difference is: as Figure 11 As shown, several groups of disk-shaped planar windings 56 are provided on the right side surface of the first outer rotor moving disk 5 , and several groups of disk-type planar windings 56 are also provided on the left surface of the second outer rotor moving disk 7 .
[0096] Additionally, if Figure 10 As shown, the left side of the first outer rotor moving disk 5 is preferably provided with an annular first cooling fin 57 .
[0097] The right side of the second outer rotor moving disk 7 is preferably provided with an annular second cooling fin 75 .
PUM
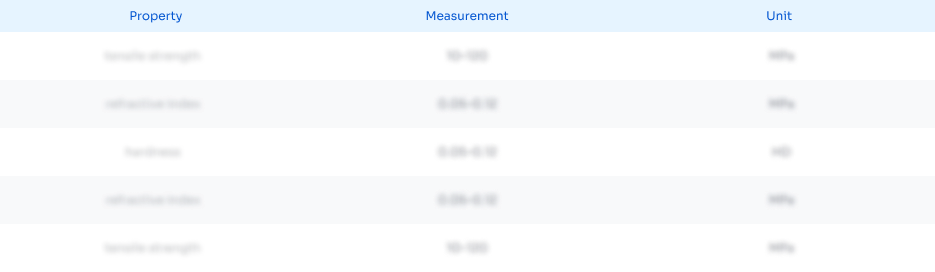
Abstract
Description
Claims
Application Information

- R&D
- Intellectual Property
- Life Sciences
- Materials
- Tech Scout
- Unparalleled Data Quality
- Higher Quality Content
- 60% Fewer Hallucinations
Browse by: Latest US Patents, China's latest patents, Technical Efficacy Thesaurus, Application Domain, Technology Topic, Popular Technical Reports.
© 2025 PatSnap. All rights reserved.Legal|Privacy policy|Modern Slavery Act Transparency Statement|Sitemap|About US| Contact US: help@patsnap.com