Quick installation method of riveting-pressing die
A riveting die and fast technology, applied in the field of mechanical manufacturing and processing, can solve the problems of wasting die changing time, unable to guarantee multiple riveting and pressing at one time, time-consuming and labor-intensive, etc., saving tool steel, installing dies and replacing dies. Convenience and improve work efficiency
- Summary
- Abstract
- Description
- Claims
- Application Information
AI Technical Summary
Problems solved by technology
Method used
Image
Examples
Embodiment Construction
[0014] Below are examples and attached figure 1 , figure 2 , image 3 The present invention is further described.
[0015] A riveting operation that needs to be completed by replacing multiple molds. Its riveting equipment is a device for quickly installing riveting molds, including: upper mold fixing seat 1, upper mold fixed punch 2, upper mold cover Barrel 3, upper die magnet 4, upper die working surface 5, lower die working face 6, lower die sleeve 7, lower die magnet 8, lower die fixed punch 9, riveting press lower die holder 10. The upper mold fixed punch 2 and the lower mold fixed punch 9 of the present invention are the same as the traditional riveting die, and one end is fixed on the upper mold fixing seat 1 or the lower mold fixing seat 10 of the riveting press, and the diameter of this end is Φ12. 6mm, the diameter of the end connected to the upper mold or the lower mold sleeve is Φ14.9mm; the upper mold sleeve 3 and the lower mold sleeve 7 both include two parts...
PUM
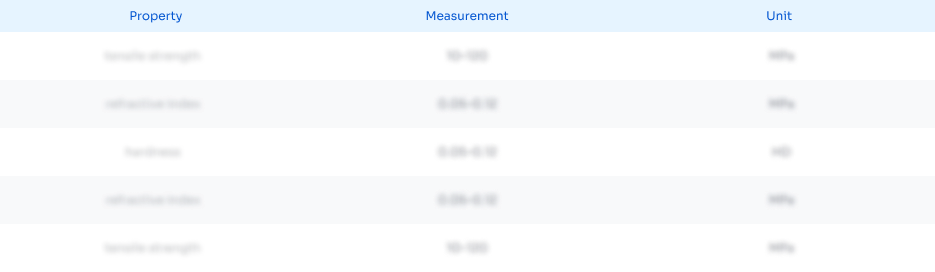
Abstract
Description
Claims
Application Information

- R&D
- Intellectual Property
- Life Sciences
- Materials
- Tech Scout
- Unparalleled Data Quality
- Higher Quality Content
- 60% Fewer Hallucinations
Browse by: Latest US Patents, China's latest patents, Technical Efficacy Thesaurus, Application Domain, Technology Topic, Popular Technical Reports.
© 2025 PatSnap. All rights reserved.Legal|Privacy policy|Modern Slavery Act Transparency Statement|Sitemap|About US| Contact US: help@patsnap.com