A control method of line anti-vibration system with adjustable resonant frequency
A technology of resonant frequency and control method, applied in the direction of mechanical vibration attenuation devices, etc., can solve the problems of high resonant frequency of overhead transmission lines and inability to match the vibration frequency of most transmission lines
- Summary
- Abstract
- Description
- Claims
- Application Information
AI Technical Summary
Problems solved by technology
Method used
Image
Examples
specific Embodiment approach 1
[0026] Specific implementation mode one: combine figure 1 with figure 2 To illustrate this embodiment, a control method of a line anti-vibration system with adjustable resonance frequency is specifically carried out according to the following steps:
[0027] The line anti-vibration system with adjustable resonance frequency includes a vibration isolator with adjustable resonance frequency and a control assembly, the control assembly is electrically connected with the vibration isolator with adjustable resonance frequency, and the vibration isolator with adjustable resonance frequency includes a line Wire clamp part 1, middle support plate 2, lower support plate 3, wire clamp buckle 4, overhead wire 5, wire protection sleeve 6, rotating rod 13, central shaft 22, screw rod 16 and stepping motor 19, line clamp part 1 The wire clip 4 is pressed onto the protective wire cover 6 set on the overhead line 5, the middle pallet 2 and the lower pallet 3 are connected with the wire clam...
specific Embodiment approach 2
[0050] Embodiment 2: The difference between this embodiment and Embodiment 1 is that the line anti-vibration control system in the step 1 is also equipped with a system reset module. When the system reset module is started, the steel strand I8 and the steel strand II23 The elongation distance between them is equal to 50%-90% of the total length of steel strand I8 or steel strand II23.
[0051] Other steps and parameters are the same as those in Embodiment 1.
specific Embodiment approach 3
[0052] Embodiment 3: The difference between this embodiment and Embodiment 1 or 2 is: in the step 1, the optical fiber vibration sensor 31 detects the value of the amplitude A1 of the steel strand I8 and the value of the amplitude A2 of the steel strand II23 for:
[0053] The value of the amplitude A1 of the detected steel strand I8 and the value of the amplitude A2 of the steel strand II23 are respectively averaged,
[0054]
[0055]
[0056] in:
[0057]
[0058] k is a natural number;
[0059] A1(i) is the sampling value of the amplitude of the steel strand I8 detected by the fiber optic vibration sensor 31 for the i time, the sampling interval is T1 / n, and i is a positive integer;
[0060] A2(i) is the sampling value of the amplitude of the steel strand II 23 detected by the optical fiber vibration sensor 31 for the ith time, the sampling interval is T1 / n, and i is a positive integer.
[0061] Other steps and parameters are the same as those in Embodiment 1 or ...
PUM
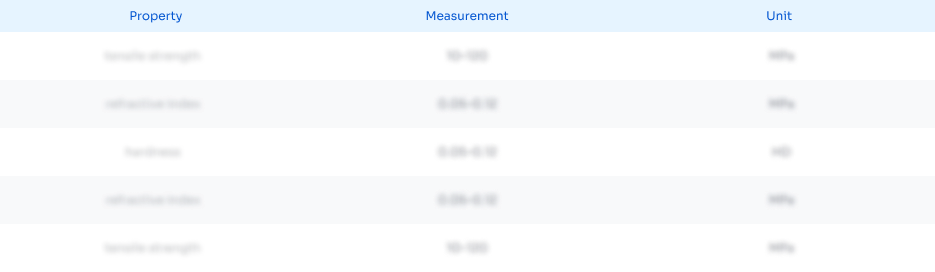
Abstract
Description
Claims
Application Information

- R&D
- Intellectual Property
- Life Sciences
- Materials
- Tech Scout
- Unparalleled Data Quality
- Higher Quality Content
- 60% Fewer Hallucinations
Browse by: Latest US Patents, China's latest patents, Technical Efficacy Thesaurus, Application Domain, Technology Topic, Popular Technical Reports.
© 2025 PatSnap. All rights reserved.Legal|Privacy policy|Modern Slavery Act Transparency Statement|Sitemap|About US| Contact US: help@patsnap.com