Welding stress frame used for light enclosure wall structure of vessel
A welding pressure and surrounding wall technology, applied in welding equipment, auxiliary welding equipment, welding/cutting auxiliary equipment, etc., can solve the problems of long turnover period, large welding workload, danger of lifting and transporting weights, etc., and reduce welding construction. Cost, stable welding performance, and the effect of ensuring welding quality
- Summary
- Abstract
- Description
- Claims
- Application Information
AI Technical Summary
Problems solved by technology
Method used
Image
Examples
Embodiment 1
[0027] Such as figure 1 As shown, the welding pressure frame of the light enclosure structure of the ship in this embodiment includes a conveying system for transporting the light enclosure structure 11 of the ship and a fixed welding for fixing and welding the light enclosure structure 11 of the ship. system, the fixed welding system is arranged across the upper part of the conveying system, the fixed welding system includes a welding gantry 4 arranged across the conveying system, a welding trolley 5 is arranged above the beam of the welding gantry 4, The bottom of the beam is provided with a compression hydraulic cylinder 6 for compressing the ship's light enclosure structure 11 from above, and also includes a support system for compressing the ship's light enclosure structure 11 from below. The supporting platform 7 on the conveying system and the platen structure 8 arranged on the supporting platform 7 .
[0028] The welded pressure frame of the light enclosure wall struc...
PUM
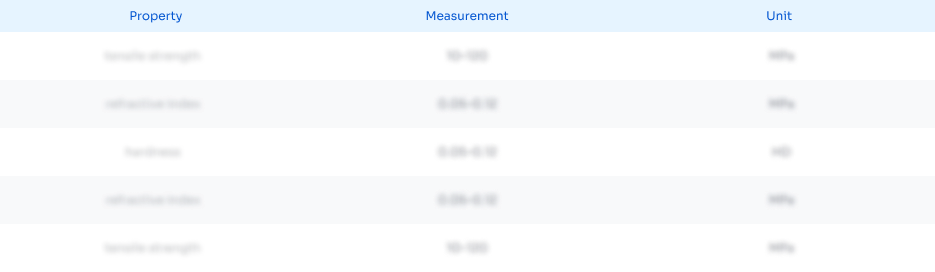
Abstract
Description
Claims
Application Information

- R&D
- Intellectual Property
- Life Sciences
- Materials
- Tech Scout
- Unparalleled Data Quality
- Higher Quality Content
- 60% Fewer Hallucinations
Browse by: Latest US Patents, China's latest patents, Technical Efficacy Thesaurus, Application Domain, Technology Topic, Popular Technical Reports.
© 2025 PatSnap. All rights reserved.Legal|Privacy policy|Modern Slavery Act Transparency Statement|Sitemap|About US| Contact US: help@patsnap.com