Beam member damage recognition method based on antiresonant frequency and particle swarm optimization
An anti-resonance frequency and particle swarm algorithm technology, applied in the direction of calculation, calculation model, instrument, etc., can solve the problems of low accuracy of calculation method and difficult practical application, and achieve the effect of high accuracy and improved efficiency.
- Summary
- Abstract
- Description
- Claims
- Application Information
AI Technical Summary
Problems solved by technology
Method used
Image
Examples
Embodiment 1
[0132] Example 1 Simple supported beam calculation example
[0133] image 3 Shown is a simply supported beam model. The specific parameters of the simply supported beam in this embodiment are as follows: geometrical size span 1.0m, rectangular section height 0.1m, width 0.05m; material characteristics are 7860kg / m 3 , Modulus of elasticity 2.1×10 11 Pa. A total of 49 driving points are taken on the simulated simply supported beam, and the driving points are evenly distributed on the simply supported beam, that is, the simply supported beam is equally divided into 50 small sections with the two ends of the simply supported beam as the limit. The intersection points between each subsection (49 in total, with image 3 For example, the points labeled 2-50) are the driving points; the distances between these 49 driving points and the adjacent driving points (or the end points of the simply supported beam) are all 0.02m; subject to the boundary conditions, the distance of the simply su...
Embodiment 2
[0145] Example 2 Cantilever beam calculation example
[0146] Figure 7 Shown is a cantilever beam model, its specific geometric dimensions (including span, rectangular section height, width), material properties (including density, elastic modulus) parameters are the same as in Example 1, and the setting of driving points is also the same as in Example 1. Consistent. The applied harmonic excitation amplitude is 10N, and the frequency range is 0-530Hz.
[0147] For comprehensive verification, the following four test conditions, which are the same as those in Example 1, are set on the beam member (cantilever beam), namely:
[0148] The first working condition, denoted as D1, has no damage to the cantilever beam;
[0149] The second working condition, denoted as D2, assumes that the cantilever beam is damaged at a position 0.2m away from the left end of the beam, and the damage degree is 0.2;
[0150] In the third working condition, denoted as D3, assuming that the cantilever beam is da...
PUM
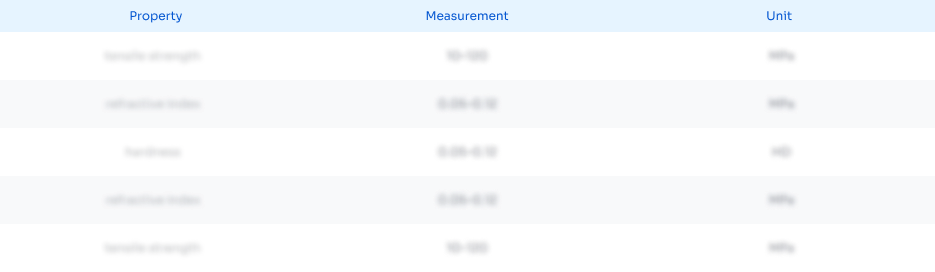
Abstract
Description
Claims
Application Information

- R&D
- Intellectual Property
- Life Sciences
- Materials
- Tech Scout
- Unparalleled Data Quality
- Higher Quality Content
- 60% Fewer Hallucinations
Browse by: Latest US Patents, China's latest patents, Technical Efficacy Thesaurus, Application Domain, Technology Topic, Popular Technical Reports.
© 2025 PatSnap. All rights reserved.Legal|Privacy policy|Modern Slavery Act Transparency Statement|Sitemap|About US| Contact US: help@patsnap.com