Hartmann sensor relay lens with multiplying power fine-adjustment mechanism
A fine-tuning mechanism and sensor technology, applied in the direction of instruments, optical components, optics, etc., can solve the problems of processing, assembly and adjustment errors, affecting the performance of Hartmann sensors, magnification errors, etc.
- Summary
- Abstract
- Description
- Claims
- Application Information
AI Technical Summary
Problems solved by technology
Method used
Image
Examples
Embodiment
[0028] Hartmann sensor relay lens with magnification fine-tuning mechanism, parameters and technical requirements are:
[0029] (1) Microlens array sub-aperture size: 0.2mm;
[0030] (2) Microlens array focal length: 7mm;
[0031] (3) CCD pixel size: 24um×24um;
[0032] (4) Number of sub-apertures: 35×35;
[0033] (5) Number of pixels occupied by a single sub-aperture: 6×6;
[0034] (6) Relay lens magnification: 0.72, and ±0.02 adjustable;
[0035] (7) Band: 486nm ~ 700nm;
[0036] (8) Total length: <150mm;
[0037] Obtained from the above requirements, the object-side numerical aperture of the relay lens is NA=0.015, and the object height is 5mm;
[0038] In the design process, Gaussian optical calculations are performed first, and the paraxial optical parameters are obtained as follows. Gaussian optical structure, such as Figure 4 Shown:
[0039] 1) The focal length of the front component: 50mm;
[0040] 2) Rear component focal length: 34.6mm;
[0041] 3) Magnific...
PUM
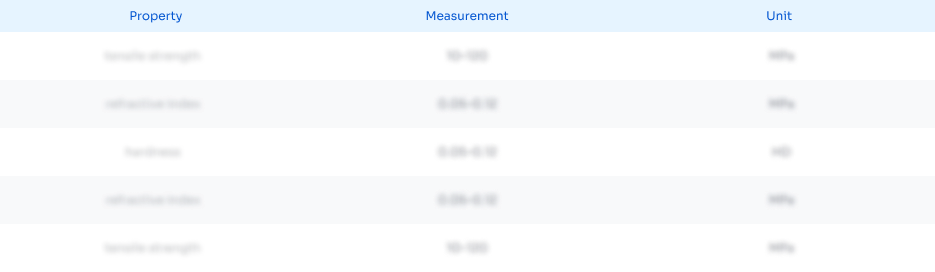
Abstract
Description
Claims
Application Information

- R&D
- Intellectual Property
- Life Sciences
- Materials
- Tech Scout
- Unparalleled Data Quality
- Higher Quality Content
- 60% Fewer Hallucinations
Browse by: Latest US Patents, China's latest patents, Technical Efficacy Thesaurus, Application Domain, Technology Topic, Popular Technical Reports.
© 2025 PatSnap. All rights reserved.Legal|Privacy policy|Modern Slavery Act Transparency Statement|Sitemap|About US| Contact US: help@patsnap.com