Copper alloy frame material strip for etching and preparation method thereof
A frame material and copper alloy technology, which is applied in the field of copper alloy frame material strips for etching and its preparation, can solve the problems of electroplating, packaging and other processes that cannot be carried out smoothly, distortion, warping, etc., and achieve the reduction of residual internal stress and low The effect of simple cost and process
- Summary
- Abstract
- Description
- Claims
- Application Information
AI Technical Summary
Problems solved by technology
Method used
Examples
Embodiment 1
[0021] Alloy composition: Ni2.3%, Si0.5%; Mg0.1%; Fe0.05%; Mn0.002%; Zn0.005%; Cu97.043%.
[0022] Add other components to the molten copper liquid, and after mixing uniformly, perform casting. The ingot is hot rolled at 950°C, and the strip (16mm) after rolling at 700°C is quenched at a cooling rate of 25°C / s.
[0023] Cold rolled to 2.5mm thickness for second phase precipitation strengthening annealing (530℃, 6h), then cold rolled to 1.0mm thickness for recrystallization annealing (480℃, 7h), and then cold rolled to preform thickness 0.4mm thickness annealing (450℃, 6h), the finished product is rolled to 0.127mm.
[0024] Perform tension correction (elongation rate 0.35%, tension in the tension correction zone 300N / mm 2 , Winding tension 40N / mm 2 ) Improve the plate shape, low-temperature heat treatment (temperature 400℃, time 25s), and at the same time, carry out surface cleaning treatment to obtain the finished strip.
Embodiment 2
[0026] Alloy composition: Ni3.2%, Si0.75%; Mg0.25%; Fe0.2%; Mn0.01%; Zn0.015%; Cu95.575%.
[0027] The other components are added to the molten copper liquid, and after the mixing is uniform, the casting is performed. The ingot is hot rolled at 950°C, and the strip (16mm) after rolling at 700°C is quenched at a cooling rate of 25°C / s.
[0028] Cold rolled to 2.5mm thickness for second phase precipitation strengthening annealing (530°C, 6h), then cold rolled to 1.0mm thickness for recrystallization annealing (480°C, 7h), and then cold rolled to a thickness of 0.4mm for pre-finished product thickness annealing (450℃, 6h), the finished product is rolled to 0.127mm.
[0029] Perform tension straightening (elongation rate 0.35%, tension in the tension straightening zone 300N / mm 2 , Winding tension 40N / mm 2 ) Improve the plate shape, low-temperature heat treatment (temperature 400℃, time 25s), and at the same time, carry out surface cleaning treatment to obtain the finished strip.
Embodiment 3
[0031] Alloy composition: Ni2.5%, Si0.55%; Mg0.08%; Fe0.1%; Mn0.005%; Zn0.008%; Cu96.757%.
[0032] The other components are added to the molten copper liquid, and after the mixing is uniform, the casting is performed. The ingot is hot rolled at 980°C, and the strip (16mm) after rolling at 720°C is quenched at a cooling rate of 25°C / s.
[0033] Cold rolled to 2.0mm thickness for second phase precipitation strengthening annealing (530°C, 6h), then cold rolled to 1.0mm thickness, recrystallization annealing (480°C, 7h), and then cold rolled to preform thickness 0.3mm thickness annealing (450℃, 6h), the finished product is rolled to 0.127mm.
[0034] Perform tension correction (elongation rate 0.35%, tension in the tension correction zone 300N / mm 2 , Winding tension 40N / mm 2 ) Improve the plate shape, low-temperature heat treatment (anneal temperature 400℃, time 30s), and at the same time, carry out surface cleaning treatment to obtain strip products.
PUM
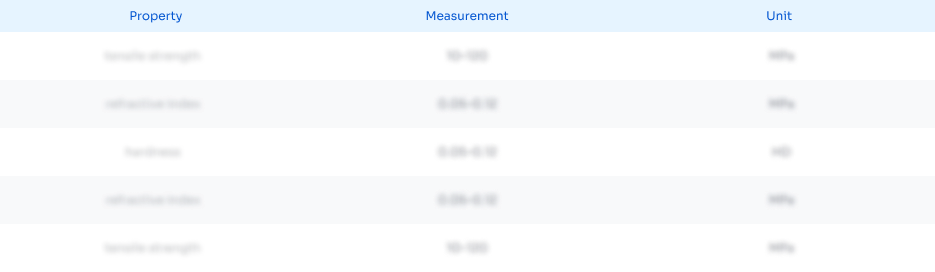
Abstract
Description
Claims
Application Information

- R&D
- Intellectual Property
- Life Sciences
- Materials
- Tech Scout
- Unparalleled Data Quality
- Higher Quality Content
- 60% Fewer Hallucinations
Browse by: Latest US Patents, China's latest patents, Technical Efficacy Thesaurus, Application Domain, Technology Topic, Popular Technical Reports.
© 2025 PatSnap. All rights reserved.Legal|Privacy policy|Modern Slavery Act Transparency Statement|Sitemap|About US| Contact US: help@patsnap.com