Full penetration weld method for fillet joint single-face J-shaped groove of box beam of vibration screen
A technology of groove and beam angle, which is applied in the direction of welding equipment, arc welding equipment, workpiece edge, etc., can solve the problems of inability to guarantee weld penetration, weld incomplete fusion, and not allow the use of permanent backing plates, etc., to achieve The effect of simplifying the welding process, ensuring consistency, and reducing overall production costs
- Summary
- Abstract
- Description
- Claims
- Application Information
AI Technical Summary
Problems solved by technology
Method used
Image
Examples
Embodiment Construction
[0022] The present invention will be further described below in conjunction with accompanying drawing:
[0023] Such as Figure 1 to Figure 4 As shown, a single-sided J-shaped groove full-penetration welding method for a vibrating screen box beam corner joint, including the following steps:
[0024] 1) A general-purpose welding robot with linear positioning function is selected, and the welding robot has the function of teaching the welding path trajectory. Specifically, the KR16-2 welding robot of KUKA Company is selected;
[0025] 2) The commissioning test plate is taken from the base metal body, and the welding process qualification test is carried out through the commissioning test plate, and finally determine the control indicators of the influencing factors of the formation of the weld pool and the quantitative elements of the technical characteristics, including the groove type and size, The control indicators of the quantitative elements formed by the position of the ...
PUM
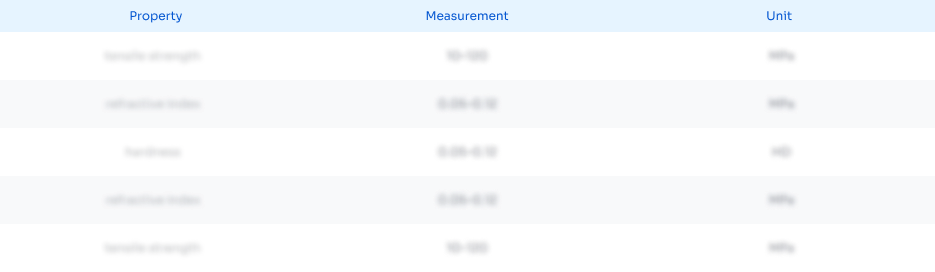
Abstract
Description
Claims
Application Information

- Generate Ideas
- Intellectual Property
- Life Sciences
- Materials
- Tech Scout
- Unparalleled Data Quality
- Higher Quality Content
- 60% Fewer Hallucinations
Browse by: Latest US Patents, China's latest patents, Technical Efficacy Thesaurus, Application Domain, Technology Topic, Popular Technical Reports.
© 2025 PatSnap. All rights reserved.Legal|Privacy policy|Modern Slavery Act Transparency Statement|Sitemap|About US| Contact US: help@patsnap.com