Corner streamhandling method for double-layer injection molding of LED light-guide components
A light guide component and double-layer injection molding technology, applied in the field of automobile lamp manufacturing, can solve problems such as low pass rate, affecting product molding quality, and inability to discharge
- Summary
- Abstract
- Description
- Claims
- Application Information
AI Technical Summary
Problems solved by technology
Method used
Image
Examples
Embodiment
[0062] A corner flow treatment method for double-layer injection molding of an LED light guide component uses a double-layer injection mold that is divided into two injection moldings and is used for injection molding thick-walled light guide components. The thick-walled light guide member is composed of a "convex" section of the product and a "concave" section matching the "convex" section.
[0063] The double-layer injection mold includes a “convex” primary injection cavity portion corresponding to the cross-sectional shape of the product and a secondary injection cavity portion with a “concave” cross-sectional shape, that is, the primary injection cavity is used for Forming the "convex" portion of the light guiding member, the overmolded cavity is used to form a "female" portion that mates with the "convex" portion of the light guiding member. The secondary injection molding cavity is used to form the wall thickness of the cavity between the inner and outer sides of the "co...
PUM
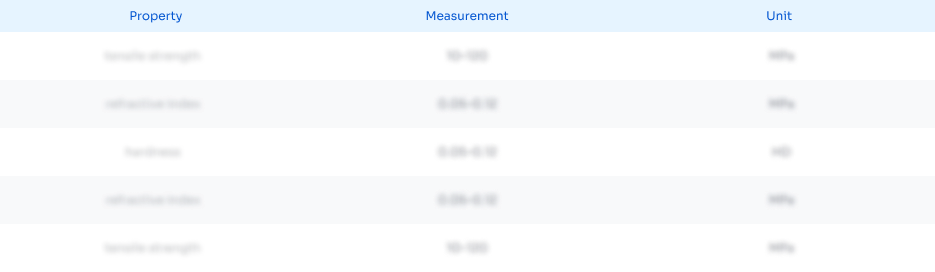
Abstract
Description
Claims
Application Information

- R&D Engineer
- R&D Manager
- IP Professional
- Industry Leading Data Capabilities
- Powerful AI technology
- Patent DNA Extraction
Browse by: Latest US Patents, China's latest patents, Technical Efficacy Thesaurus, Application Domain, Technology Topic, Popular Technical Reports.
© 2024 PatSnap. All rights reserved.Legal|Privacy policy|Modern Slavery Act Transparency Statement|Sitemap|About US| Contact US: help@patsnap.com