Static loading test device for missile wing
A test device and static loading technology, which is applied in the direction of applying stable tension/pressure to test the strength of materials, etc., can solve the problems of complex structure of electro-hydraulic servo loading device, structural damage of the elastic wing test piece, and high safety hazards. The effect of ensuring the consistency of the test state, improving the automation level and operation efficiency, and reducing the operation intensity
- Summary
- Abstract
- Description
- Claims
- Application Information
AI Technical Summary
Problems solved by technology
Method used
Image
Examples
Embodiment Construction
[0058] figure 1 It is the overall structure diagram of the static loading test device of the elastic wing of the present invention, which is mainly composed of the scissor mechanism 1, the buffer pillar 2, the basic platform 4, the trough guide rail 5, the lifting platform 6, the weight 8, and the load-bearing soft sling 10 , Wrap belt 11, elastic wing 12, elastic wing clamp 13, bearing column 15, fixed pulley 16, upper limit travel switch 17, reel mechanism 18, two-stage gear reducer 19, electric motor 20, electric control box 21, wire rope Cable 22, guide wheels 23, cover plate 24, lower limit travel switch 27 and other components.
[0059] In specific implementation, such as figure 1 with 2 As shown, the structural features and connection relationships of the main components are as follows:
[0060] ①The foundation platform 4 is formed by tailor-welding of several channel steel 35 and steel plates. The adapter plate 38 is welded on the side of the foundation platform 4, and the ...
PUM
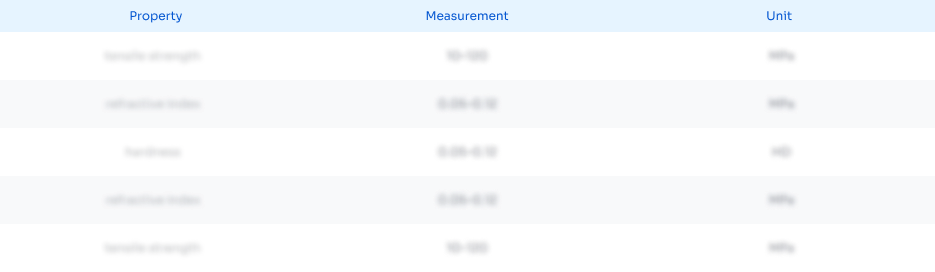
Abstract
Description
Claims
Application Information

- Generate Ideas
- Intellectual Property
- Life Sciences
- Materials
- Tech Scout
- Unparalleled Data Quality
- Higher Quality Content
- 60% Fewer Hallucinations
Browse by: Latest US Patents, China's latest patents, Technical Efficacy Thesaurus, Application Domain, Technology Topic, Popular Technical Reports.
© 2025 PatSnap. All rights reserved.Legal|Privacy policy|Modern Slavery Act Transparency Statement|Sitemap|About US| Contact US: help@patsnap.com