Cable climbing robot
A robot and cable climbing technology, applied in the field of robots, can solve the problems of unable to change the robot's holding force to the cable, unable to control the robot's recovery, unable to use the cable, etc. Effect
- Summary
- Abstract
- Description
- Claims
- Application Information
AI Technical Summary
Problems solved by technology
Method used
Image
Examples
specific Embodiment approach
[0033] Figure 1-4 It is shown that a specific implementation of the present invention is: a cable climbing robot, including an outer frame 400 and an internal crawling mechanism, the structure of which is:
[0034] The outer frame 400 is a cubic frame. Between the uprights on each side of the outer frame 400, the ball screws 401 whose two ends rotate in opposite directions are connected by bearings. The two opposite ball screws 401 are fixed on the outer frame 400 by one Stepper motor 402 drive;
[0035] Each side of the outer frame 400 is provided with a sliding frame 200. The specific structure of the sliding frame 200 is as follows: two vertical rods are connected by a cross rod, and the upper and lower ends of the vertical rods are equipped with a sliding guide wheel 201. The guide wheel 201 is in contact with the top rod and the bottom rod of the outer frame 300 respectively; the outer sides of the two vertical rods are both fixed with a screw nut 202 that matches with the b...
PUM
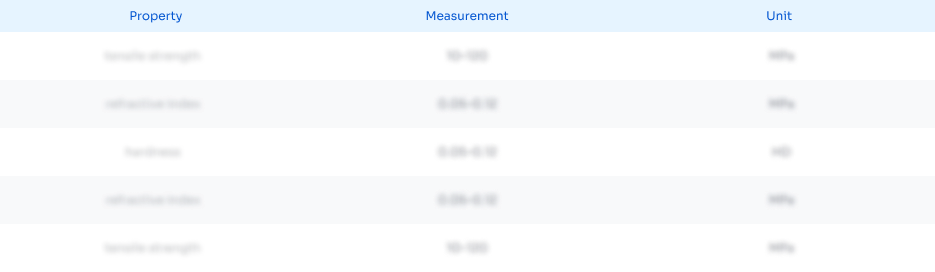
Abstract
Description
Claims
Application Information

- R&D
- Intellectual Property
- Life Sciences
- Materials
- Tech Scout
- Unparalleled Data Quality
- Higher Quality Content
- 60% Fewer Hallucinations
Browse by: Latest US Patents, China's latest patents, Technical Efficacy Thesaurus, Application Domain, Technology Topic, Popular Technical Reports.
© 2025 PatSnap. All rights reserved.Legal|Privacy policy|Modern Slavery Act Transparency Statement|Sitemap|About US| Contact US: help@patsnap.com