Control device for rolling stock drive device
一种驱动装置、控制装置的技术,应用在传动装置控制、通用动力装置的多个不同原动机的布置、动力装置等方向,能够解决发热量增大、时间长等问题,达到减少变速次数、减少能量损失、提高能量效率的效果
- Summary
- Abstract
- Description
- Claims
- Application Information
AI Technical Summary
Problems solved by technology
Method used
Image
Examples
no. 1 approach >
[0045]
[0046] Such as figure 1 as well as figure 2 As shown, a hybrid vehicle (hereinafter, simply referred to as a vehicle) 1 has a rotating electric machine (hereinafter, referred to as a motor generator or simply a motor) 3 as a drive source in addition to an internal combustion engine 2 . The hybrid drive device 100 as a vehicle drive device constituting the drive train of the vehicle 1 is a single-motor type hybrid drive device, and includes a transmission mechanism 6 arranged on a transmission path between the internal combustion engine 2 and the wheels 4, and The input unit 5 between the transmission mechanism 6 and the internal combustion engine 2 is constituted.
[0047] Speed change mechanism 6 such as figure 2 Shown has a plurality of engagement elements (more specifically, a plurality of frictional engagement elements) C-1 to C-3, B-1, B-2, F-1, and the card through these plurality of engagement elements A multi-speed automatic transmission (stepped auto...
no. 2 approach >
[0096] Next, according to Figure 9 to Figure 11 A vehicle control device according to a second embodiment of the present invention will be described. In addition, the second embodiment is different in that the estimated temperature of the frictional engagement element at the time of shifting is calculated, and whether the skip shift can be performed is determined based on whether the estimated temperature is higher than the allowable temperature. Therefore, in the following description, only the points of difference from the above-mentioned first embodiment will be described, and descriptions of other parts will be omitted.
[0097] Figure 9 It is a graph showing the transition of the estimated temperature of the main body side frictional engagement element while the vehicle is running. exist Figure 9 It can be seen that the frictional engagement element on the main body side is engaged and switched at time t1-t2 and time t3-t4, and generates heat due to transmission of ...
no. 3 approach >
[0106] In the above-mentioned second embodiment, whether or not the skip shift can be performed is determined based on all the requirements of the calorific value, the estimated temperature, and the shift time. However, for example, the skip shift may be judged based only on the calorific value. Can it be implemented. Of course, it is also possible to determine whether skip shifting can be performed based only on the estimated temperature requirement, and it is also possible to determine whether skip shifting can be performed based only on these calorific value requirements and the estimated temperature requirement.
[0107] In addition, in the above-mentioned first to third embodiments, a hybrid drive device has been described as an example of a drive device for a vehicle. However, an engine is not necessarily required as a drive source. As long as it is a vehicle with a rotary electric machine on the input side of the transmission mechanism, The present invention can be appl...
PUM
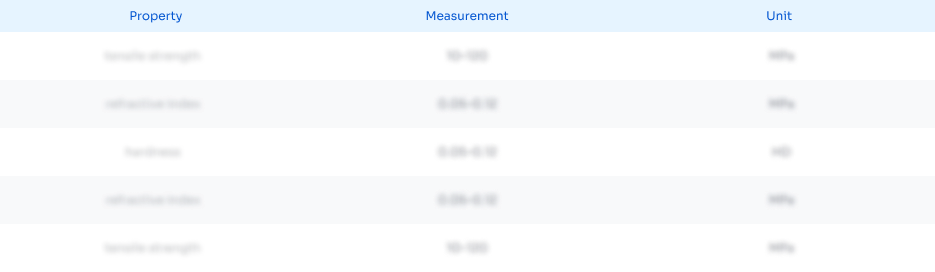
Abstract
Description
Claims
Application Information

- R&D Engineer
- R&D Manager
- IP Professional
- Industry Leading Data Capabilities
- Powerful AI technology
- Patent DNA Extraction
Browse by: Latest US Patents, China's latest patents, Technical Efficacy Thesaurus, Application Domain, Technology Topic, Popular Technical Reports.
© 2024 PatSnap. All rights reserved.Legal|Privacy policy|Modern Slavery Act Transparency Statement|Sitemap|About US| Contact US: help@patsnap.com