Method for removing ink of waste paper
A waste paper deinking and waste paper technology, which is applied in the field of pulp and paper making, can solve the problems of less types of surfactants and environmental pollution, and achieve the effects of less residual amount, simplified process flow and high yield
- Summary
- Abstract
- Description
- Claims
- Application Information
AI Technical Summary
Problems solved by technology
Method used
Image
Examples
Embodiment 1
[0020] S1. Waste paper pulping and deinking: Put the waste paper into the pulper, add deinking agent and other chemical auxiliary materials in turn into the pulper, add hot water and control the pulp concentration to 15%, and the pulping temperature is 65°C, pulping time 25min. The addition amount of this deinking agent is 1.3‰ of waste paper by weight percentage; The addition amount of described chemical auxiliary material is 5% of waste paper by weight percentage, and this chemical auxiliary material includes caustic soda, water glass, hydrogen peroxide, and the weight ratio is 2 :3:1. The deinking agent is prepared according to the following steps: according to the weight percentage, the following components are weighed: fatty alcohol polyoxyethylene ether is 12%, sodium dodecylbenzenesulfonate is 43%, Tween 80 is 2%, water is 43%; then stir to mix.
[0021] S2. Deslagging and concentration: the crushed slurry is put into the slag remover for slagging, and the slag remove...
Embodiment 2
[0024] S1. Waste paper pulping and deinking: Put the waste paper into the pulper, add deinking agent and other chemical auxiliary materials in sequence in the pulper, add hot water and control the pulp concentration to 17%, and the pulping temperature is 68°C, pulping time 30min. The addition of the deinking agent is 1.5‰ of the waste paper by weight percentage; the addition of the chemical auxiliary material is 6% of the waste paper by weight percentage, and the chemical auxiliary material includes caustic soda, water glass, hydrogen peroxide, and the weight ratio is 2 :3:1. The deinking agent is prepared according to the following steps: according to the weight percentage, the following components are weighed: fatty alcohol polyoxyethylene ether is 15%, sodium dodecylbenzenesulfonate is 43%, Tween 80 is 2%, water is 40%; then stir to mix.
[0025] S2. Deslagging and concentration: the crushed slurry is put into the slag remover for slagging, and the slag removed slurry ent...
Embodiment 3
[0028] S1. Waste paper pulping and deinking: Put the waste paper into the pulper, add deinking agent and other chemical auxiliary materials in turn into the pulper, add hot water and control the pulp concentration to 18%, and the pulping temperature is 65°C, pulping time 28min. The addition of the deinking agent is 1.5‰ of the waste paper by weight percentage; the addition of the chemical auxiliary material is 6% of the waste paper by weight percentage, and the chemical auxiliary material includes caustic soda, water glass, hydrogen peroxide, and the weight ratio is 2 :3:1. The deinking agent is prepared according to the following steps: according to the percentage by weight, the following components are weighed: fatty alcohol polyoxyethylene ether is 10%, sodium dodecylbenzenesulfonate is 43%, Tween 80 is 2%, water is 45%; then stir to mix.
[0029] S2. Deslagging and concentration: the crushed slurry is put into the slag remover for slagging, and the slag removed slurry en...
PUM
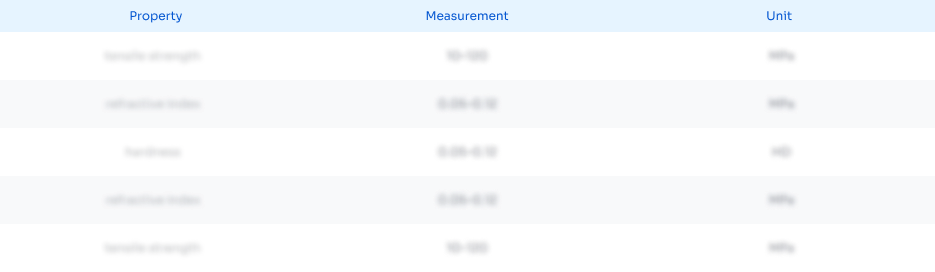
Abstract
Description
Claims
Application Information

- Generate Ideas
- Intellectual Property
- Life Sciences
- Materials
- Tech Scout
- Unparalleled Data Quality
- Higher Quality Content
- 60% Fewer Hallucinations
Browse by: Latest US Patents, China's latest patents, Technical Efficacy Thesaurus, Application Domain, Technology Topic, Popular Technical Reports.
© 2025 PatSnap. All rights reserved.Legal|Privacy policy|Modern Slavery Act Transparency Statement|Sitemap|About US| Contact US: help@patsnap.com