Polyester composite material for nano injection molding and preparation method thereof
A polyester composite material and nano-injection molding technology, applied in the field of composite materials, can solve problems such as complex preparation methods, achieve simple and easy preparation methods, be suitable for large-scale production applications, and improve the bonding strength
- Summary
- Abstract
- Description
- Claims
- Application Information
AI Technical Summary
Problems solved by technology
Method used
Image
Examples
Embodiment 1
[0025] The components in Table 1 are mixed in a mixer according to the weight ratio shown in Table 1, and then granulated with a twin-screw extruder at a granulation temperature between 220°C and 250°C. The obtained particles are processed by injection molding according to the standards and methods in the Japanese Taisei Chemical patent and the binding force is tested. The test results are shown in Table 1.
[0026] Table 1
[0027]
[0028] Wherein EVA is ethylene-vinyl acetate copolymer.
[0029] From the comparison of the reference and the sample in Table 1, it can be seen that the addition of other polyesters can greatly improve the bonding force between the PBT-based polyester composite and metal. And as the content of other polyesters increases, the binding force is further improved. This is mainly because the crystallization rate of other polyesters is significantly lower than that of PBT, and their addition can reduce the overall crystallization rate of the syste...
Embodiment 2
[0031] The components in Table 2 were mixed in a mixer according to the weight ratio shown in Table 2, and then granulated with a twin-screw extruder at a granulation temperature between 220°C and 250°C. The obtained particles were processed by injection molding according to the standards and methods described in the specification and the binding force was tested. The test results are shown in Table 2.
[0032] Table 2
[0033]
[0034] Wherein EVA is ethylene-vinyl acetate copolymer.
[0035] In Example 2, Sample 5 in Example 1 was used as a reference. It can be seen from the data in Table 2 that when metal salt compounds are added to the system, the binding force between plastic and metal is significantly improved, and the binding force will increase with the increase of the metal salt compound content, especially when the metal salt compound When the content of the content reaches more than 0.5%, the binding force is obviously improved. This is mainly because the met...
PUM
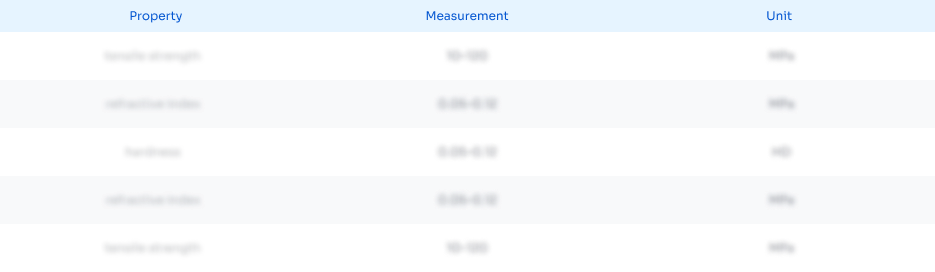
Abstract
Description
Claims
Application Information

- Generate Ideas
- Intellectual Property
- Life Sciences
- Materials
- Tech Scout
- Unparalleled Data Quality
- Higher Quality Content
- 60% Fewer Hallucinations
Browse by: Latest US Patents, China's latest patents, Technical Efficacy Thesaurus, Application Domain, Technology Topic, Popular Technical Reports.
© 2025 PatSnap. All rights reserved.Legal|Privacy policy|Modern Slavery Act Transparency Statement|Sitemap|About US| Contact US: help@patsnap.com