Full-automatic production line for forming corrugated boards
A fully automatic, production line technology, applied in forming tools, feeding devices, manufacturing tools, etc., can solve the problems of bending machine errors, restricting the quality and production efficiency of corrugated board forming, and affecting the quality and accuracy of corrugated board forming.
- Summary
- Abstract
- Description
- Claims
- Application Information
AI Technical Summary
Problems solved by technology
Method used
Image
Examples
Embodiment Construction
[0009] The fully automatic production line for forming corrugated boards of the present invention includes a molding machine and a sheet material conveying device. Such as figure 2As shown, the press includes a portal frame 72 . An upper mold guide seat 67 is respectively provided on the horizontal left and right sides columns of the door-shaped support 72 . Upper mold 57 is installed between two upper mold guide seats 67, and upper mold 57 is provided with upper mold mounting plate 58, and upper mold 57 is slidably matched with upper mold guide seat 67 by upper mold mounting plate 58. The upper part of the door-shaped support 72 is provided with a molding cylinder 64, the piston rod of the molding cylinder 64 is connected with the upper mold mounting plate 58, and the molding cylinder 64 can drive the upper mold 57 to move vertically relative to the upper mold guide seat 67 to realize pressurization. forming. The lower part of the gate-shaped support 72 is provided with a...
PUM
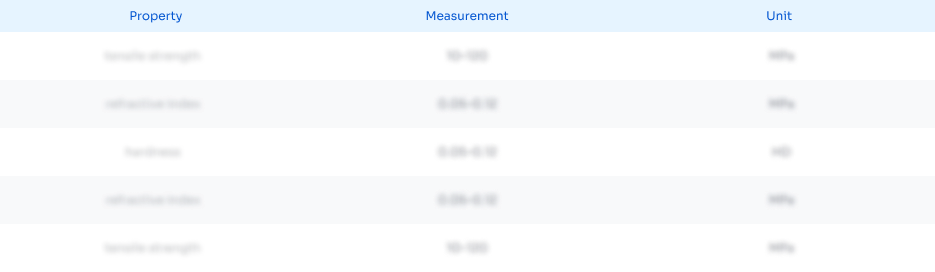
Abstract
Description
Claims
Application Information

- R&D
- Intellectual Property
- Life Sciences
- Materials
- Tech Scout
- Unparalleled Data Quality
- Higher Quality Content
- 60% Fewer Hallucinations
Browse by: Latest US Patents, China's latest patents, Technical Efficacy Thesaurus, Application Domain, Technology Topic, Popular Technical Reports.
© 2025 PatSnap. All rights reserved.Legal|Privacy policy|Modern Slavery Act Transparency Statement|Sitemap|About US| Contact US: help@patsnap.com