Adaptive time-delay feedback control micromachined gyroscope system
A technology of micro-mechanical gyroscope and feedback control, applied in gyroscope/steering sensing equipment, gyroscope effect for speed measurement, instrument and other directions, can solve the problem of system stability reduction and possible bifurcation and chaos, system damping complexity, stability Higher performance requirements and other issues, to achieve the effect of improving detection accuracy, adaptability and stability, and improving anti-interference ability
- Summary
- Abstract
- Description
- Claims
- Application Information
AI Technical Summary
Problems solved by technology
Method used
Image
Examples
Embodiment Construction
[0018] The self-adaptive time-delay feedback control micromechanical gyroscope system of the present invention, especially the time-delay feedback control of the electrostatically driven resonant micromechanical gyroscope, the electrostatic comb drive and the electrostatic comb capacitance and parallel plate capacitance are jointly detected, including temperature Compensation and acceleration compensation and sensitive direction amplitude feedback, through the frequency amplitude and waveform modulation of the driving voltage by the microprocessor.
[0019] figure 1 Shown is a schematic diagram of the structure of a single resonant mass indirectly connected, where the X-axis direction of the coordinates is the driving direction, the Y-axis direction is the detection direction, Ωz is the input angular velocity direction, 1 is the detection direction parallel plate capacitor fixed plate, and 2 is the parallel plate Capacitive movable plate, the sensitive direction adopts paralle...
PUM
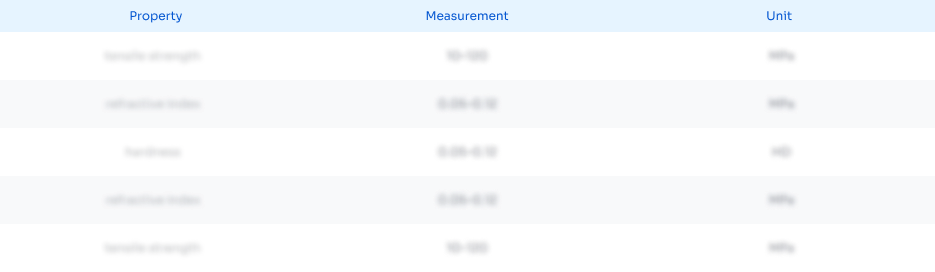
Abstract
Description
Claims
Application Information

- Generate Ideas
- Intellectual Property
- Life Sciences
- Materials
- Tech Scout
- Unparalleled Data Quality
- Higher Quality Content
- 60% Fewer Hallucinations
Browse by: Latest US Patents, China's latest patents, Technical Efficacy Thesaurus, Application Domain, Technology Topic, Popular Technical Reports.
© 2025 PatSnap. All rights reserved.Legal|Privacy policy|Modern Slavery Act Transparency Statement|Sitemap|About US| Contact US: help@patsnap.com