Low-cotton-droppings processing technology for cotton spinning combing machine
A processing technology and combing machine technology, applied in the direction of combing machine, textile and papermaking, fiber processing, etc., can solve the problems of coarse combed yarn count and low quality requirements.
- Summary
- Abstract
- Description
- Claims
- Application Information
AI Technical Summary
Problems solved by technology
Method used
Image
Examples
Embodiment 1
[0025] A processing technology for cotton spinning comber low noil, achieved through the following steps:
[0026] (1) On the pre-draw frame in the combing preparation process, increase the number of fed slivers, increase the total draft multiple and the rear zone draft multiple.
[0027] The feeding number of sliver on the pre-draw frame is changed from 5-6 to 7-8, the total draft ratio is changed from 4-6 times to 7-8 times, and the draft ratio in the rear area is changed from the original Adjust the 1.6-1.8 times to 1.8-2.1 times, so as to improve the fiber structure such as fiber straightness, parallelism and separation degree of pre-drawing.
[0028] (2) On the sliver doubling machine in the combing preparation process, increase the number of slivers to be combined and increase the total draft multiple.
[0029] The combined number of slivers on the sliver doubling machine is adjusted from 20-24 to 24-32, and the total draft ratio is adjusted from 1.4-1.7 to 1.6-2.4.
...
Embodiment approach
[0044] (1) On the pre-draw frame of the combing preparation process, 8 cotton slivers are merged. The total draft ratio of the draw frame is set to 8 times, and the draft ratio in the rear area is set to 2.1 times.
[0045] (2) On the sliver doubling machine, the number of slivers combined is 32, and the total draft ratio is 2.4 times.
[0046] (3) On the combing machine in the combing process, the quantitative setting of the cotton lap fed to the combing machine is set to 75 g / m, and the cotton feeding length of each working cycle of the combing machine is set to 5.9 mm.
[0047] (4) Set the cotton feeding mechanism of the combing machine to the forward feeding mode, and adjust the position of the cotton feeding roller to the front limit position.
[0048] (5) Change the crank radius OA of the rocker mechanism driven by the pendulum shaft of the comber nipper from the original 50mm to 75mm.
[0049] (6) Set the noil gauge of the comber to 6.5mm.
[0050] (7) The combing pro...
PUM
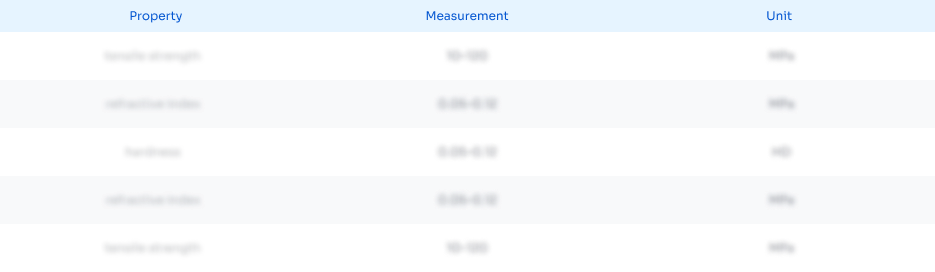
Abstract
Description
Claims
Application Information

- R&D Engineer
- R&D Manager
- IP Professional
- Industry Leading Data Capabilities
- Powerful AI technology
- Patent DNA Extraction
Browse by: Latest US Patents, China's latest patents, Technical Efficacy Thesaurus, Application Domain, Technology Topic, Popular Technical Reports.
© 2024 PatSnap. All rights reserved.Legal|Privacy policy|Modern Slavery Act Transparency Statement|Sitemap|About US| Contact US: help@patsnap.com