A hot-dip galvanizing process
A process method and hot-dip galvanizing technology, applied in hot-dip plating process, metal material coating process, coating and other directions, can solve the problems of high zinc consumption, poor appearance quality, poor fluidity of zinc liquid, etc., to achieve high efficiency, low cost effect
- Summary
- Abstract
- Description
- Claims
- Application Information
AI Technical Summary
Problems solved by technology
Method used
Image
Examples
Embodiment Construction
[0046] The preferred embodiments of the present invention will be described in detail below in conjunction with the accompanying drawings.
[0047] see figure 1 , figure 1 It is a hot-dip galvanizing process method of the present invention, and its process steps are as follows:
[0048] (1) Inspection before plating
[0049] According to the size and shape of workpieces, they are sorted and stacked;
[0050] Check the workpiece for cracks and defects;
[0051] The workpiece must have a hanging position or a hole position, and for hollow workpieces such as pipes, vent holes or zinc flow holes are required;
[0052] The impurities and welding slag on the surface of the workpiece should be cleaned up;
[0053] (2) pendant
[0054] According to the size, length, shape and binding method of the workpiece, identify and select special slings or slings for hanging;
[0055] (3) Washing
[0056] Lift the workpiece into the washing tank and pull it up and down for 3-4 times. Aft...
PUM
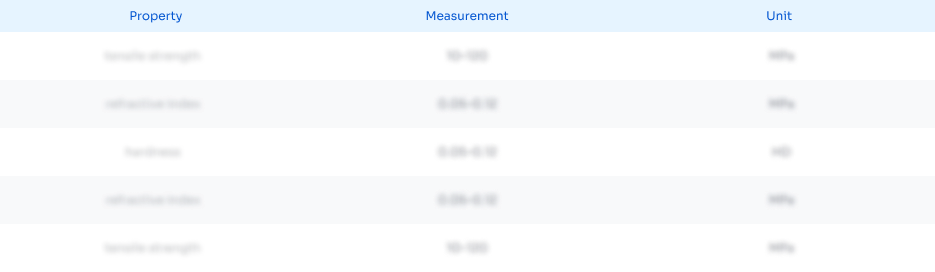
Abstract
Description
Claims
Application Information

- R&D
- Intellectual Property
- Life Sciences
- Materials
- Tech Scout
- Unparalleled Data Quality
- Higher Quality Content
- 60% Fewer Hallucinations
Browse by: Latest US Patents, China's latest patents, Technical Efficacy Thesaurus, Application Domain, Technology Topic, Popular Technical Reports.
© 2025 PatSnap. All rights reserved.Legal|Privacy policy|Modern Slavery Act Transparency Statement|Sitemap|About US| Contact US: help@patsnap.com