Modified kaolin as well as preparation method and application thereof
A kaolin and modification technology, applied in the field of modified kaolin and its preparation, can solve the problems of layered structure damage, unfavorable cost and energy consumption, kaolin cracking reaction performance and heavy oil cracking performance without particularly obvious effect, etc., to achieve pore distribution Effects of improvement, low energy consumption and operating cost, heavy oil cracking capacity and increased activity and gasoline yield
- Summary
- Abstract
- Description
- Claims
- Application Information
AI Technical Summary
Problems solved by technology
Method used
Image
Examples
Embodiment approach
[0020] According to a preferred embodiment of the present invention, preferably the kaolin of the present invention is prepared according to the following steps: uniformly mix the kaolin raw material and aqueous sulfuric acid solution, and perform the first heat treatment on the obtained mixture; wash and filter the solid after the first heat treatment, The filtered solids are subjected to a second heat treatment.
[0021] The method for modifying kaolin provided by the present invention does not need to roast kaolin at a high temperature above 700°C to transform it into metakaolin, so the energy consumption and operating cost are relatively low, and the prepared modified kaolin has at least the aforementioned properties of the present invention. Compared with the catalyst made of unmodified kaolin, the heavy oil cracking ability, activity and gasoline yield of the cracking catalyst used as a carrier have been significantly improved. It can be seen that the method of the prese...
Embodiment 1
[0035]Kaolin (produced by Suzhou Kaolin Industry Co., Ltd., whose chemical composition is shown in Table 1, the following examples and comparative examples are the same) and sulfuric acid aqueous solution (concentration is 85% by weight) according to the weight of sulfuric acid: kaolin (on a dry basis) = 0.4:1 Mix evenly, put the resulting mixture in a muffle furnace and dry at 150°C for 1.5 hours, take out the product after cooling, then slurry and wash the product with deionized water 5 times the weight of the original kaolin at 80°C for 40 minutes, filter After being pumped into a filter cake, it was washed with deionized water 5 times the weight of the original kaolin, and the filtered product was dried at 120°C for 12 hours.
Embodiment 2
[0037] Mix kaolin and sulfuric acid aqueous solution (concentration: 98% by weight) according to the weight ratio of sulfuric acid: kaolin (on a dry basis) = 0.5:1, put the resulting mixture in a muffle furnace and roast at 240°C for 1.5 hours, take it out after cooling product, then the product was slurried and washed at 80°C for 40 minutes with deionized water 5 times the weight of the original kaolin and filtered, then the filter cake was washed with deionized water 5 times the weight of the original kaolin and filtered, after filtration The product was dried at 120°C for 12 hours, and the obtained modified kaolin sample was recorded as B-2, and its physical and chemical characterization results are listed in Table 1.
PUM
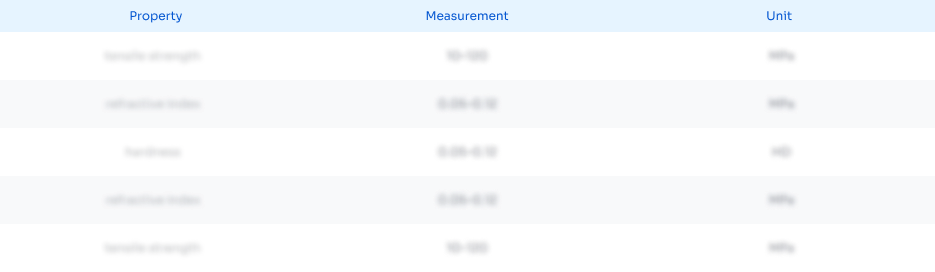
Abstract
Description
Claims
Application Information

- R&D Engineer
- R&D Manager
- IP Professional
- Industry Leading Data Capabilities
- Powerful AI technology
- Patent DNA Extraction
Browse by: Latest US Patents, China's latest patents, Technical Efficacy Thesaurus, Application Domain, Technology Topic, Popular Technical Reports.
© 2024 PatSnap. All rights reserved.Legal|Privacy policy|Modern Slavery Act Transparency Statement|Sitemap|About US| Contact US: help@patsnap.com