Carbon fiber bicycle disc brake base and its forming process
A carbon fiber base and bicycle technology, applied in bicycle accessories, bicycle brakes, etc., can solve the problems of damaged carbon fiber, poor product disc brake size, and affecting the strength of the base, so as to avoid damage, reduce secondary processing procedures, and ensure strength effect on longevity
- Summary
- Abstract
- Description
- Claims
- Application Information
AI Technical Summary
Problems solved by technology
Method used
Image
Examples
Embodiment approach
[0020] Such as Figure 3 to Figure 5 As shown, the present invention discloses a carbon fiber bicycle disc brake base, which includes a carbon fiber base 1 and a cylindrical nut 2. The carbon fiber base 1 is provided with two protruding feet 11, and the two protruding feet 11 are respectively provided with cylindrical nuts 2, and integrated with the carbon fiber base 1 to form a carbon fiber bicycle disc brake base.
[0021] The specific molding process of the carbon fiber bicycle disc brake base is:
[0022] Step 1. Design and process the cylindrical nut 2 with thread;
[0023] Step 2. Prefabricate the base 1 of the carbon fiber bicycle disc brake, and at the same time embed the column nuts 2 into the two protruding feet 11 of the prefabricated carbon fiber base 1;
[0024] Step 3. Place the base 1 of the carbon fiber bicycle disc brake with the pre-embedded cylindrical nut 2 in the mold A, lock the cylindrical nut 2 with the screw 3 and fix it in the positioning cavity of the mold ...
PUM
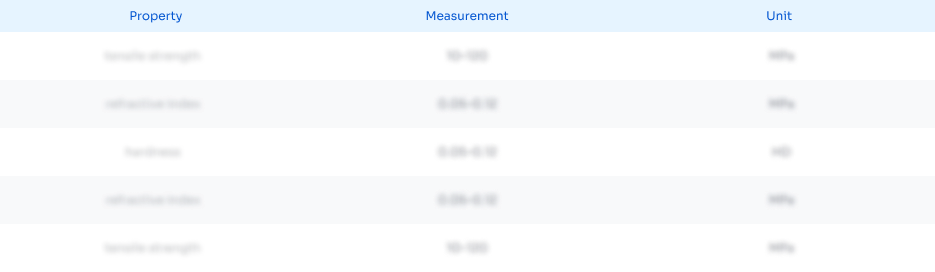
Abstract
Description
Claims
Application Information

- R&D
- Intellectual Property
- Life Sciences
- Materials
- Tech Scout
- Unparalleled Data Quality
- Higher Quality Content
- 60% Fewer Hallucinations
Browse by: Latest US Patents, China's latest patents, Technical Efficacy Thesaurus, Application Domain, Technology Topic, Popular Technical Reports.
© 2025 PatSnap. All rights reserved.Legal|Privacy policy|Modern Slavery Act Transparency Statement|Sitemap|About US| Contact US: help@patsnap.com