Automatic three-dimensional measuring method and automatic three-dimensional measuring system for high-precision blade of aviation engine
An aero-engine, three-dimensional measurement technology, applied in the field of precision measurement, can solve the problems of measurement results, low measurement accuracy, and measurement data accuracy.
- Summary
- Abstract
- Description
- Claims
- Application Information
AI Technical Summary
Problems solved by technology
Method used
Image
Examples
Embodiment Construction
[0059] In order to make the object, technical solution and advantages of the present invention clearer, the present invention will be further described in detail below in conjunction with the accompanying drawings and embodiments. It should be understood that the specific embodiments described here are only used to explain the present invention, not to limit the present invention. In addition, the technical features involved in the various embodiments of the present invention described below can be combined with each other as long as they do not constitute a conflict with each other.
[0060] Such as figure 1 As shown, a high-precision automatic three-dimensional measurement system for aeroengine blades includes a motion support platform 1; a three-axis motion mechanism 2 installed on the motion support platform 1; a rotary table 3 installed on the three-axis motion mechanism 2; The tooling 4 is installed on the rotary table 3, including the cylindrical section and the fixtur...
PUM
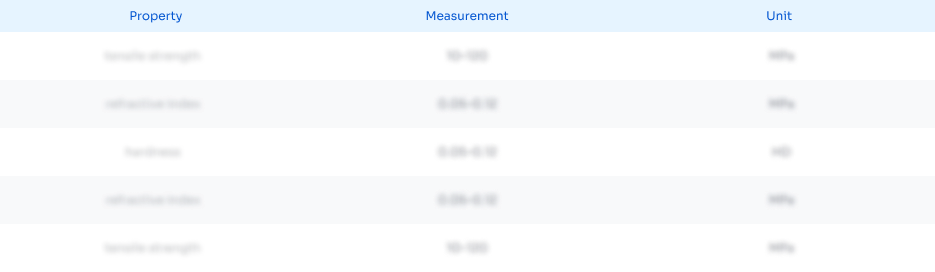
Abstract
Description
Claims
Application Information

- R&D
- Intellectual Property
- Life Sciences
- Materials
- Tech Scout
- Unparalleled Data Quality
- Higher Quality Content
- 60% Fewer Hallucinations
Browse by: Latest US Patents, China's latest patents, Technical Efficacy Thesaurus, Application Domain, Technology Topic, Popular Technical Reports.
© 2025 PatSnap. All rights reserved.Legal|Privacy policy|Modern Slavery Act Transparency Statement|Sitemap|About US| Contact US: help@patsnap.com