Catalytic cracking method and device
A catalytic cracking device and catalytic cracking technology, applied in the direction of catalytic cracking, chemical instruments and methods, cracking, etc., can solve the problems of lowering the temperature of the regenerated catalyst, short oil agent contact time, difficult to achieve, etc., to achieve improved properties, short oil agent The effect of exposure time
- Summary
- Abstract
- Description
- Claims
- Application Information
AI Technical Summary
Problems solved by technology
Method used
Image
Examples
Embodiment 1
[0068] The main operating conditions and product distribution of Examples 1-5 are shown in Table 4. The main properties of the liquid product of Example 1 are shown in Table 5, the main properties of the liquid product of Example 2 are shown in Table 6, the main properties of the liquid product of Example 3 are shown in Table 7, and the main properties of the liquid product of Example 4 are shown in Table 8. The main properties of liquid products of 5 are shown in Table 9.
[0069] Table 1 Heavy oil raw material properties (comparative example, embodiment 1~5)
[0070] Heavy Oil Raw Materials
Daqing Atmospheric Residue
Density (20℃), kg·m -3
900.2
Charcoal residue, %
4.2
Family composition, %
saturated hydrocarbon
62.3
Aromatics
22.6
Colloid + asphaltenes
15.1
Sulfur content, μg g -1
1450
Ni, μg g -1
4.3
V, μg·g -1
0.2
[0071] The main operating co...
PUM
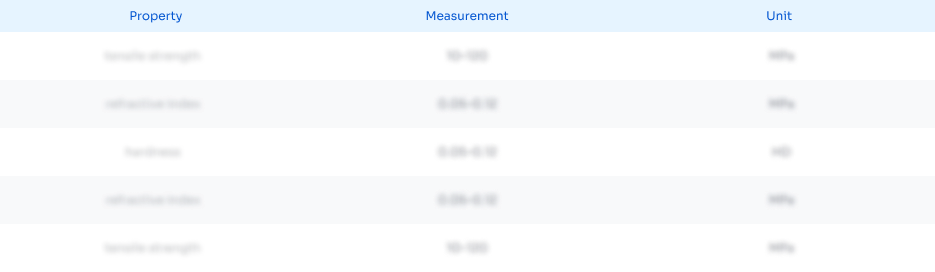
Abstract
Description
Claims
Application Information

- R&D
- Intellectual Property
- Life Sciences
- Materials
- Tech Scout
- Unparalleled Data Quality
- Higher Quality Content
- 60% Fewer Hallucinations
Browse by: Latest US Patents, China's latest patents, Technical Efficacy Thesaurus, Application Domain, Technology Topic, Popular Technical Reports.
© 2025 PatSnap. All rights reserved.Legal|Privacy policy|Modern Slavery Act Transparency Statement|Sitemap|About US| Contact US: help@patsnap.com