A secondary ejection die-casting mold
A die-casting mold and secondary ejection technology, which is applied in the field of die-casting molds, can solve problems such as product production difficulties, affecting the airtightness of molded products, and easy breakage of inserts, so as to solve the problem of insufficient ejection force for mold opening and improve the quality of die-casting , to avoid the effect of product sticking mold
- Summary
- Abstract
- Description
- Claims
- Application Information
AI Technical Summary
Problems solved by technology
Method used
Image
Examples
Embodiment 1
[0038] like Figure 1 to Figure 10 As shown, a secondary ejection die-casting mold of the present invention includes a template, an insert pin 3, a thimble 4, a back pin 5, a front thimble plate 6, a rear thimble plate 7 and a bottom plate 8, and the template includes a first rear template 1 and The second rear template 2, the setting needle 3 is connected with the second rear template 2, the thimble 4 is connected with the front thimble plate 6, the return needle 5 is connected with the rear thimble plate 7, and the bottom plate 8 is arranged under the rear thimble plate 7. A limit pop-up device 20 is arranged between the ejector plate 7 and the front ejector plate 6, and the limit pop-up device 20 includes an upper limit block 21, a middle limit block 22 and a lower limit block 23, and the upper limit block 21 is connected to the front ejector plate 6. connection, the middle limit block 22 is elastically connected with the rear thimble plate 7, the lower limit block 23 is co...
Embodiment 2
[0045] like Figure 11 As shown, the difference between the present embodiment and the first embodiment is that a blind hole 32 is opened in the insert needle 3, and a water barrier 31 is arranged in the blind hole 32, and the water barrier 31 separates the blind hole 32 to form A cooling water circuit; specifically, the cooling water is passed into the cooling water circuit, and the cooling water can cool the insert 3 during the flow of the cooling water circuit, thereby preventing the castable from sticking to the insert 3, Avoid shrinkage and air holes in the product, increase the airtightness of the product at the position of the pin 3, and further improve the yield and quality of the product.
[0046] In this embodiment, the cooling water circuit includes a water inlet 33 and a water outlet 34, the water inlet 33 is connected with a water inlet pipe, and the water outlet 34 is connected with a water outlet pipe, and the cooling water passes into the water inlet 33 from th...
PUM
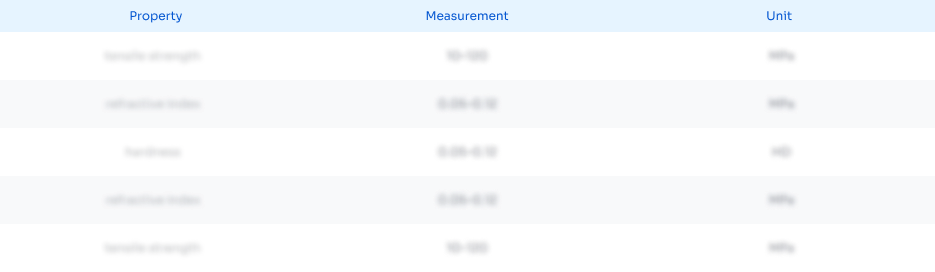
Abstract
Description
Claims
Application Information

- R&D Engineer
- R&D Manager
- IP Professional
- Industry Leading Data Capabilities
- Powerful AI technology
- Patent DNA Extraction
Browse by: Latest US Patents, China's latest patents, Technical Efficacy Thesaurus, Application Domain, Technology Topic, Popular Technical Reports.
© 2024 PatSnap. All rights reserved.Legal|Privacy policy|Modern Slavery Act Transparency Statement|Sitemap|About US| Contact US: help@patsnap.com