A kind of ethylene-vinyl acetate copolymer/polypyrrole composite conductive material and preparation method thereof
A technology of vinyl acetate and composite conduction, which is applied in the field of composite conductive materials, can solve the problems of weak combination and low conductivity of composite materials, and achieve the effects of easy realization of preparation process conditions, excellent conductivity, and increased specific surface area
- Summary
- Abstract
- Description
- Claims
- Application Information
AI Technical Summary
Problems solved by technology
Method used
Image
Examples
Embodiment 1
[0028] After mixing 700 grams of EVA and 300 grams of PEO, melt and granulate through a twin-screw extruder at a temperature of 160° C., and the speed of the twin-screw extruder is 100 rpm to obtain EVA / PEO blended pellets. Put the EVA / PEO pellets into the mold, hot press in a flat bed for 30 minutes, the molding temperature is 150°C, and the pressure is 15MPa to obtain the EVA / PEO blend film. The blended membrane was placed in water at 30° C., and the PEO was dissolved at a constant temperature for 4 hours to obtain a porous EVA membrane.
[0029] 15 grams of EVA porous membranes are added to 500 parts by weight of 0.1mol / L pyrrole aqueous solution, and after stirring for 0.5 hours, 100 grams of 0.1mol / L iron sesquioxide aqueous solution is added dropwise to the reaction solution, and the dropping time is 0.5 hours After the dropwise addition, continue to react for 0.5 hours to complete the reaction. During the whole process, the temperature of the reaction system is maintain...
Embodiment 2
[0031] After mixing 600 grams of EVA and 400 grams of PEO, melt and granulate through a twin-screw extruder at a temperature of 150° C., and the speed of the twin-screw extruder is 200 rpm to obtain EVA / PEO blended pellets. Put the EVA / PEO pellets into the mold, hot press in a flat bed for 20 minutes, the molding temperature is 140°C, and the pressure is 15MPa to obtain the EVA / PEO blend film. The blended membrane was placed in water at 60° C., and the PEO was dissolved at a constant temperature for 2 hours to obtain a porous EVA membrane.
[0032] 20 grams of EVA porous membranes are added to 500 parts by weight of 0.5mol / L pyrrole aqueous solution, and after stirring for 0.5 hours, 250 grams of 0.7mol / L iron sesquioxide aqueous solution is added dropwise to the reaction solution, and the dropping time is 0.5 hours After the dropwise addition, the reaction was continued for 4 hours to complete the reaction. During the whole process, the temperature of the reaction system was ...
Embodiment 3
[0034] After mixing 700 grams of EVA and 300 grams of PEO, melt and granulate through a twin-screw extruder at a temperature of 160° C., and the speed of the twin-screw extruder is 300 rpm to obtain EVA / PEO blended pellets. Put the EVA / PEO pellets into the mold, hot press in a flat bed for 30 minutes, the molding temperature is 150°C, and the pressure is 15MPa to obtain the EVA / PEO blend film. The blended membrane was placed in water at 80° C., and the PEO was dissolved at a constant temperature for 1 hour to obtain a porous EVA membrane.
[0035] 15 grams of EVA porous membranes are added to 500 parts by weight of 0.7mol / L pyrrole aqueous solution, and after stirring for 0.5 hours, 300 grams of 1.0mol / L iron sesquioxide aqueous solution is added dropwise to the reaction solution, and the dropping time is 0.5 hours After the dropwise addition, the reaction was continued for 3 hours to complete the reaction. During the whole process, the temperature of the reaction system was m...
PUM
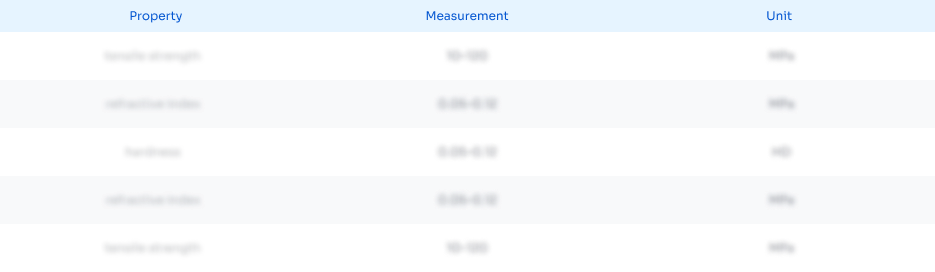
Abstract
Description
Claims
Application Information

- Generate Ideas
- Intellectual Property
- Life Sciences
- Materials
- Tech Scout
- Unparalleled Data Quality
- Higher Quality Content
- 60% Fewer Hallucinations
Browse by: Latest US Patents, China's latest patents, Technical Efficacy Thesaurus, Application Domain, Technology Topic, Popular Technical Reports.
© 2025 PatSnap. All rights reserved.Legal|Privacy policy|Modern Slavery Act Transparency Statement|Sitemap|About US| Contact US: help@patsnap.com