A Quasi-Zero Stiffness Vibration Isolator Using Ring Permanent Magnets to Generate Negative Stiffness
A technology of quasi-zero stiffness and permanent magnets, which is applied in the field of vibration isolators, can solve problems such as the hysteretic effect of the supporting spring, large static deformation of the supporting spring, and reduce the stiffness of the system, achieving good uniformity and weak nonlinear effects
- Summary
- Abstract
- Description
- Claims
- Application Information
AI Technical Summary
Problems solved by technology
Method used
Image
Examples
Embodiment Construction
[0025] The present invention will be described in further detail below in combination with specific embodiments.
[0026] Such as figure 1 As shown, the present invention uses a ring-shaped permanent magnet to generate a quasi-zero stiffness vibration isolator with negative stiffness, including a base 1, and an outer cylinder 4 connected to the base 1 through a first bolt 3, and the bottom of the inner wall of the outer cylinder 4 has a ring The bottom gap, the base 1 and the outer cylinder 4 are provided with a base boss 2 at the corresponding position, the bottom gap of the outer cylinder 4 matches the shape of the base boss 2 of the base 1, and the base boss 2 of the base 1 is stuck on the outer cylinder 4 On the bottom notch of the base, ensure the centering of the base 1 and the outer cylinder 4. Such as figure 2 As shown, the top of the inner wall of the outer cylinder 4 has a top gap, and the outer permanent magnet 7 is placed in the top gap. The upper cover 9 is co...
PUM
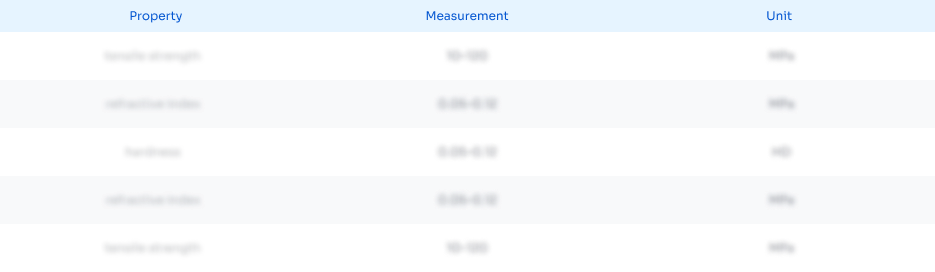
Abstract
Description
Claims
Application Information

- R&D
- Intellectual Property
- Life Sciences
- Materials
- Tech Scout
- Unparalleled Data Quality
- Higher Quality Content
- 60% Fewer Hallucinations
Browse by: Latest US Patents, China's latest patents, Technical Efficacy Thesaurus, Application Domain, Technology Topic, Popular Technical Reports.
© 2025 PatSnap. All rights reserved.Legal|Privacy policy|Modern Slavery Act Transparency Statement|Sitemap|About US| Contact US: help@patsnap.com