Flash smelting method of laterite nickel ore
A lateritic nickel ore and flash smelting technology, which is applied in the field of metallurgy, can solve the problems that the content of nickel and cobalt is difficult to exceed 20%, the product value is not high, and the selection effect is small, so as to avoid sticking phenomenon, improve reduction efficiency, and improve The effect of recovery
- Summary
- Abstract
- Description
- Claims
- Application Information
AI Technical Summary
Problems solved by technology
Method used
Image
Examples
Embodiment 1
[0046] Such as figure 1 As shown, purchase the laterite nickel ore raw material powder with a particle size of 150 microns; add pulverized coal and oxygen into the laterite nickel ore smelting furnace with a diameter of 4 meters, control the temperature in the suspension smelting chamber to 1200 degrees Celsius, and contain 78-82% reduction Reducing atmosphere of gas: Coal oxygen is sprayed into the smelting chamber through the nozzle of the molten pool, the temperature in the molten pool is controlled to be 1430 degrees Celsius, the reducing atmosphere contains 83-87% reducing gas, and the smelting time in the molten pool is controlled to be 30 minutes.
[0047] By calculation, the nickel content in the product reaches 10%.
Embodiment 2
[0049] Such as figure 1 As shown, purchase the laterite nickel ore raw material powder with a particle size of 150 microns; add pulverized coal and oxygen into the laterite nickel ore smelting furnace with a diameter of 4 meters, control the temperature in the suspension smelting chamber to 1150 degrees Celsius, and contain 38-42% reduction Reducing atmosphere of gas: Coal oxygen is sprayed into the smelting chamber through the molten pool nozzle, the temperature in the molten pool is controlled to be 1430 degrees Celsius, the reducing atmosphere contains 83-87% reducing gas, and the smelting time in the molten pool is controlled to be 20 minutes.
[0050] By calculation, the nickel content in the product has reached 20%.
Embodiment 3
[0052] Such as figure 1 As shown, purchase the laterite nickel ore raw material powder with a particle size of 150 microns; add pulverized coal and oxygen to the laterite nickel ore smelting furnace with a diameter of 4 meters, control the temperature in the suspension smelting chamber to 1150 degrees Celsius, and contain 23-27% reduction The reducing atmosphere of gas: inject coal oxygen into molten pool 22 through molten pool nozzle, control the temperature in molten pool to be 1430 degrees centigrade, contain the reducing atmosphere of 83~87% reducing gas, control the smelting time in molten pool to be 10 minutes.
[0053] According to calculations, in the suspension smelting chamber, the iron in the laterite nickel ore is basically not reduced; after smelting in the molten pool, the content of nickel and cobalt in the obtained product reaches 40%.
PUM
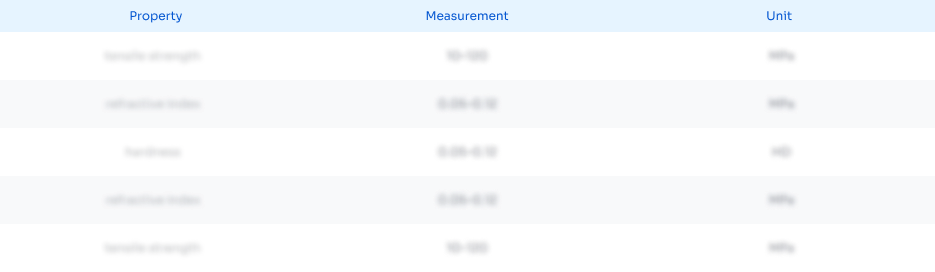
Abstract
Description
Claims
Application Information

- Generate Ideas
- Intellectual Property
- Life Sciences
- Materials
- Tech Scout
- Unparalleled Data Quality
- Higher Quality Content
- 60% Fewer Hallucinations
Browse by: Latest US Patents, China's latest patents, Technical Efficacy Thesaurus, Application Domain, Technology Topic, Popular Technical Reports.
© 2025 PatSnap. All rights reserved.Legal|Privacy policy|Modern Slavery Act Transparency Statement|Sitemap|About US| Contact US: help@patsnap.com