A kind of EPDM rubber material for wire and cable and preparation method thereof
A technology of EPDM rubber, wire and cable, applied in the direction of rubber insulators, organic insulators, etc., can solve the problems of poor processability and inability to meet actual use requirements, and achieve the effects of improved strength performance, low production cost, and convenient processing
- Summary
- Abstract
- Description
- Claims
- Application Information
AI Technical Summary
Problems solved by technology
Method used
Examples
Embodiment 1
[0031] The EPDM material for electric wire and cable of the present invention has its distribution ratio of each component in parts by weight:
[0032] (1) 100 parts of EPDM rubber,
[0033] (2) 7 parts of acrylic acid,
[0034] (3) 5 parts of sodium stearate,
[0035] (4) 3 parts of initiator,
[0036] (5) 3 parts of anti-aging agent,
[0037] (6) 0.8 part of inorganic filler,
[0038] (7) 1.5 parts of flame retardant.
[0039] The initiator is dicumyl peroxide.
[0040] The anti-aging agent is anti-aging agent MB.
[0041] The inorganic filler is white carbon black, and the flame retardant is ammonium polyphosphate.
[0042] The preparation method of EPDM rubber material for said electric wire and cable, it may further comprise the steps:
[0043] (1) Pre-mix EPDM rubber, acrylic acid and sodium stearate by heating at a temperature of 55°C.
[0044] (2) Then the initiator, anti-aging agent, inorganic filler and flame retardant are heated and mixed with the mixture i...
Embodiment 2
[0048] The EPDM material for electric wire and cable of the present invention, its distribution ratio of each component in parts by weight:
[0049] (1) 105 parts of EPDM rubber,
[0050] (2) 8 parts of acrylic acid,
[0051] (3) 5 parts of sodium stearate,
[0052] (4) 4 parts of initiator,
[0053] (5) 4 parts of anti-aging agent,
[0054] (6) 0.9 part of inorganic filler,
[0055] (7) 1.2 parts of flame retardant.
[0056] The initiator is dicumyl peroxide.
[0057] The anti-aging agent is anti-aging agent MB.
[0058] The inorganic filler is pottery clay, and the flame retardant is ammonium polyphosphate.
[0059] The preparation method of EPDM rubber material for said electric wire and cable, it may further comprise the steps:
[0060] (1) Pre-mix EPDM rubber, acrylic acid and sodium stearate by heating at a temperature of 53°C.
[0061] (2) Then the initiator, anti-aging agent, inorganic filler and flame retardant are heated and mixed with the mixture in step (1...
Embodiment 3
[0065] The EPDM material for electric wire and cable of the present invention, its distribution ratio of each component in parts by weight:
[0066] (1) 119 parts of EPDM rubber,
[0067] (2) 6 parts of acrylic acid,
[0068] (3) 3 parts of sodium stearate,
[0069] (4) 5 parts of initiators,
[0070] (5) 7 parts of anti-aging agent,
[0071] (6) 1.2 parts of inorganic filler,
[0072] (7) 1.0 parts of flame retardant.
[0073] The initiator is dicumyl peroxide.
[0074] The anti-aging agent is anti-aging agent MB.
[0075] The inorganic filler is pottery clay, and the flame retardant is ammonium polyphosphate.
[0076] The preparation method of EPDM rubber material for said electric wire and cable, it may further comprise the steps:
[0077] (1) Pre-mix EPDM rubber, acrylic acid, and sodium stearate by heating at a temperature of 52°C.
[0078] (2) Then the initiator, anti-aging agent, inorganic filler and flame retardant are heated and mixed with the mixture in step...
PUM
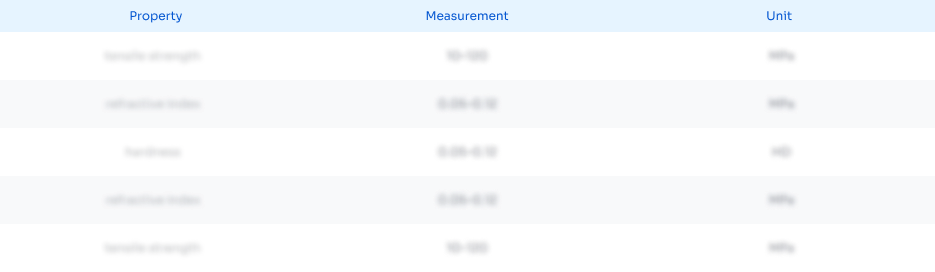
Abstract
Description
Claims
Application Information

- R&D Engineer
- R&D Manager
- IP Professional
- Industry Leading Data Capabilities
- Powerful AI technology
- Patent DNA Extraction
Browse by: Latest US Patents, China's latest patents, Technical Efficacy Thesaurus, Application Domain, Technology Topic, Popular Technical Reports.
© 2024 PatSnap. All rights reserved.Legal|Privacy policy|Modern Slavery Act Transparency Statement|Sitemap|About US| Contact US: help@patsnap.com