A robot joint with variable stiffness
A technology of robot joints and robots, applied in the field of robots, to achieve the effect of strong practicability, simple structure and small pre-tightening force
- Summary
- Abstract
- Description
- Claims
- Application Information
AI Technical Summary
Problems solved by technology
Method used
Image
Examples
Embodiment Construction
[0028] The present invention will be further described below in conjunction with the accompanying drawings and specific embodiments, but not as a limitation of the present invention.
[0029] see figure 1 , the robot joint with variable stiffness, including the transition end 1, the transition end 1 is located in the next link of the reducer in the robot joint transmission chain, and plays the role of connecting the reducer and the output end-2, and transmits the motion of the reducer, which is the joint motion input terminal. The auxiliary friction plate 3 is connected with the output end 1 of the reducer through the concave surface and the external teeth, the auxiliary friction plate 5 is connected with the output end 2 6 through the concave surface and the external teeth, and the main friction plate 4 is clamped between the auxiliary friction plate 3 and the auxiliary friction plate 5, wherein the right side of the auxiliary friction plate 3 is attached to the left side of...
PUM
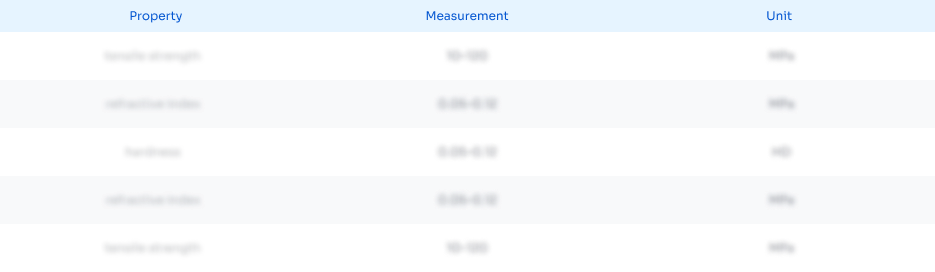
Abstract
Description
Claims
Application Information

- R&D
- Intellectual Property
- Life Sciences
- Materials
- Tech Scout
- Unparalleled Data Quality
- Higher Quality Content
- 60% Fewer Hallucinations
Browse by: Latest US Patents, China's latest patents, Technical Efficacy Thesaurus, Application Domain, Technology Topic, Popular Technical Reports.
© 2025 PatSnap. All rights reserved.Legal|Privacy policy|Modern Slavery Act Transparency Statement|Sitemap|About US| Contact US: help@patsnap.com