Welding method for furnace top flange of blast furnace
A welding method and blast furnace technology, which are applied in welding equipment, arc welding equipment, manufacturing tools, etc., can solve the problems of difficult construction, high welding quality requirements, and excessive levelness of the upper surface of the flange. Welding deformation, the effect of ensuring levelness
- Summary
- Abstract
- Description
- Claims
- Application Information
AI Technical Summary
Problems solved by technology
Method used
Image
Examples
Embodiment Construction
[0038] With reference to the attached drawings below, take 3200m 3 The installation of the furnace top flange on the blast furnace project is a specific example, and the specific implementation of the present invention will be further described.
[0039] See figure 1 , figure 2 , image 3 As shown, the elevation of the upper surface of the furnace roof flange is ▽+46.1m, the diameter of the welding seam of the furnace roof flange (the pitch circle between the furnace roof flange and the furnace roof steel ring) is φ3100mm, and the welding seam elevation is ▽+45.6m. The installation requirements are as follows:
[0040]
[0041] Among them: H is the elevation of the furnace top flange; h is the elevation of the furnace bottom; D is the diameter of the weld of the furnace top flange.
[0042] For the installation and welding of the furnace top flange, it is necessary to make preparations before construction.
[0043] Preparations before construction include:
[0044] Prepare the drawin...
PUM
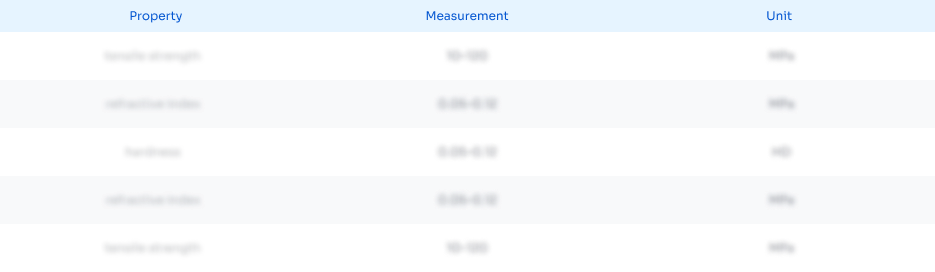
Abstract
Description
Claims
Application Information

- R&D
- Intellectual Property
- Life Sciences
- Materials
- Tech Scout
- Unparalleled Data Quality
- Higher Quality Content
- 60% Fewer Hallucinations
Browse by: Latest US Patents, China's latest patents, Technical Efficacy Thesaurus, Application Domain, Technology Topic, Popular Technical Reports.
© 2025 PatSnap. All rights reserved.Legal|Privacy policy|Modern Slavery Act Transparency Statement|Sitemap|About US| Contact US: help@patsnap.com