Novel composite plate and production method thereof
A production method and composite board technology, applied in the direction of chemical instruments and methods, layered products, packaging items, etc., can solve the problems of shortening the product life cycle, insufficient overall strength, mildew and insects, etc., to achieve guaranteed strength, Improved anti-corrosion performance and short hot-pressing time
- Summary
- Abstract
- Description
- Claims
- Application Information
AI Technical Summary
Problems solved by technology
Method used
Image
Examples
Embodiment 1
[0027] Thin wood shavings or bamboo shavings are glued, oriented paved, and hot-pressed to form a particle board 1, and the bamboo strips 2 are impregnated with phenolic resin glue and then drained, and the drained bamboo strips 2 are dried at a temperature below 90°C to The moisture content is 7%; the upper and lower surfaces of the particle board 1 are respectively covered with a layer of bamboo strips 2, and one side of the wood veneer 3 is covered with waterproof phenolic glue. Lay a piece of wood veneer 3 on the upper and lower surfaces of the strip sheet 2, respectively stick a layer of phenolic resin impregnated paper 4 on the upper and lower surfaces of the wood veneer 3, and pre-press the blank board 5 after the assembly is completed, with a pressure of 1.2Mpa, per mm of assembly The pre-pressing time of the rough plate 5 thickness is less than 1 minute; after the pre-pressed rough plate 5 is hot-pressed, the temperature is 125°C, the pressure is 2Mpa, and the hot-pres...
Embodiment 2
[0029] Thin wood shavings or bamboo shavings are glued, oriented paved, and hot-pressed to form a particle board 1, and the bamboo strips 2 are impregnated with phenolic resin glue and then drained, and the drained bamboo strips 2 are dried at a temperature below 90°C to The moisture content is 18%; the upper and lower surfaces of the particle board 1 are respectively covered with a layer of bamboo strips 2, and one side of the wood veneer 3 is covered with waterproof phenolic glue. 2 Lay a piece of wood veneer 3 on the upper and lower surfaces respectively, and stick a layer of phenolic resin impregnated paper on the upper and lower surfaces of the wood veneer 3 respectively. 5. The thickness pre-pressing time is less than 1 minute; after the pre-pressed rough plate 5 is hot-pressed, the temperature is 145°C, the pressure is 3Mpa, and the hot-pressing time for each millimeter of the rough plate 5 thickness is less than 1.5 minutes, sawing, milling, and dividing After cutting,...
Embodiment 3
[0031] Thin wood shavings or bamboo shavings are glued, oriented paved, and hot-pressed to form a particle board 1, and the bamboo strips 2 are impregnated with phenolic resin glue and then drained, and the drained bamboo strips 2 are dried at a temperature below 90°C to The moisture content is 10%; the upper and lower surfaces of the particle board 1 are respectively covered with a layer of bamboo strips 2, and one side of the wood veneer 3 is covered with waterproof phenolic glue. A piece of wood veneer 3 is laid on the upper and lower surfaces respectively, and a layer of phenolic resin impregnated paper 4 is pasted on the upper and lower outer surfaces of the rough board of wood veneer 3 respectively. The pre-pressing time for the thickness of the board 5 is less than 1 minute; after the pre-pressed rough board 5 is hot-pressed, the temperature is 135°C, the pressure is 2.5Mpa, the hot-pressing time for each millimeter of the thickness of the rough board 5 is less than 1.5 ...
PUM
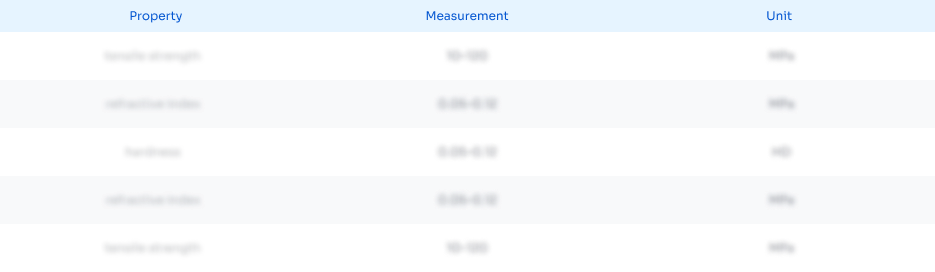
Abstract
Description
Claims
Application Information

- R&D
- Intellectual Property
- Life Sciences
- Materials
- Tech Scout
- Unparalleled Data Quality
- Higher Quality Content
- 60% Fewer Hallucinations
Browse by: Latest US Patents, China's latest patents, Technical Efficacy Thesaurus, Application Domain, Technology Topic, Popular Technical Reports.
© 2025 PatSnap. All rights reserved.Legal|Privacy policy|Modern Slavery Act Transparency Statement|Sitemap|About US| Contact US: help@patsnap.com