An ultra-precise friction drive mechanism
A friction-driven, ultra-precise technology, applied in the direction of friction transmission devices, electromechanical devices, mechanical equipment, etc., can solve the problems of many auxiliary equipment, inconvenient installation and disassembly, easy to absorb iron filings and other metal filings, etc.
- Summary
- Abstract
- Description
- Claims
- Application Information
AI Technical Summary
Problems solved by technology
Method used
Image
Examples
Embodiment Construction
[0028] The present invention will be described in detail below with reference to the accompanying drawings and in combination with embodiments.
[0029] refer to figure 1 As shown, an ultra-precision friction drive mechanism mainly includes a drive part, an auxiliary support part, a pressure applying part and an eccentric pressure applying part, and the drive part is composed of a torque motor 1 stator through a torque motor base 2 and a drive base 3 Fixed installation, the torque motor 1 rotor is connected with the friction drive shaft 4 through the motor flange 5, and is fixed by the motor fixing flange 6, the friction drive shaft 4 drive shaft is installed on the drive base 3, the drive shaft and the drive base The radial dense ball shafting system and the thrust dense ball shafting system are designed. The structure of the radial dense ball shafting system is that the dense ball bearing outer shell 7 is installed in the shaft hole of the drive base, and the steel ball 9 pa...
PUM
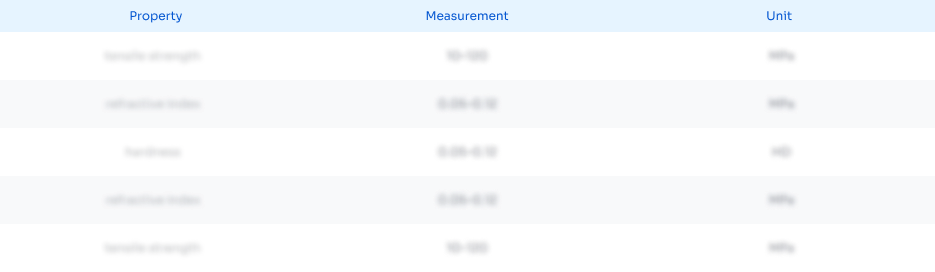
Abstract
Description
Claims
Application Information

- R&D
- Intellectual Property
- Life Sciences
- Materials
- Tech Scout
- Unparalleled Data Quality
- Higher Quality Content
- 60% Fewer Hallucinations
Browse by: Latest US Patents, China's latest patents, Technical Efficacy Thesaurus, Application Domain, Technology Topic, Popular Technical Reports.
© 2025 PatSnap. All rights reserved.Legal|Privacy policy|Modern Slavery Act Transparency Statement|Sitemap|About US| Contact US: help@patsnap.com