Technique for processing bearing ring by steel tube hot-rolling and precise cold-rolling
A technology of bearing rings and process methods, which is applied in the field of bearing rings, can solve problems that affect the development and popularization of bearing rings, difficulty in meeting the needs of the market and users, low product quality and work efficiency, and achieve saving of raw materials, Reduced labor intensity and high efficiency
- Summary
- Abstract
- Description
- Claims
- Application Information
AI Technical Summary
Problems solved by technology
Method used
Image
Examples
Embodiment 1
[0028] As shown in the figure, there is a process for processing bearing rings with hot-rolled steel pipes and precision cold rolling. The specific process steps are as follows: First, carry out the hot-rolled steel pipe process: put the round steel 1 into the electric furnace 2 according to the conventional standard Heating, and then entering the pipe threading process, the round steel 1 moves forward under the action of external force, at the same time, the moving direction of the ejector rod 3 for pipe threading is opposite to that of the round steel 1, and passes through the center of the round steel 1 under the action of external force to form a Capillary 4, complete the pipe threading process according to conventional standards; when the temperature of the capillary 4 is not completely lowered, then enter the hot rolling process; penetrate the mandrel 5 in the capillary 4 hole, and at the same time, move the capillary 4 into In the roll 12, rolling is carried out accordin...
Embodiment 2
[0031]As shown in the figure, secondly, carry out the cold rolling forming process of the bearing ring: put the hot-rolled steel pipe 6 prepared for processing the bearing ring into the automatic pipe cutting machine 7, and produce the required bearing ring material according to the processing standard requirements Section 8; Put the finished bearing ring material section 8 into the double-end surface grinder 9, grind the double-end surfaces according to the standard requirements, and then grind the outer diameter of the bearing ring material section; then, put the bearing ring material section 8 Put it into the lathe 10 and finish turning the inner diameter, and make a bearing ring blank 11 with uniform size and meet the standard for processing bearing rings; and make the inner and outer diameters of the bearing ring blank 11 smaller than the finished bearing ring size to be processed 20-35%.
Embodiment 3
[0033] As shown in the figure, in the end, the bearing ring blank 11 that is guaranteed to be unified into dimensional accuracy and 20-35% smaller than the finished bearing ring to be processed is put into the precision cold rolling forming machine 13, and is heated at normal temperature. Next, power is used to rotate the bearing ring blank 11, and increase and deform during the rotation process, and through the cold rolling forming process of the cold rolling control program, the finished bearing ring of the target size is achieved.
PUM
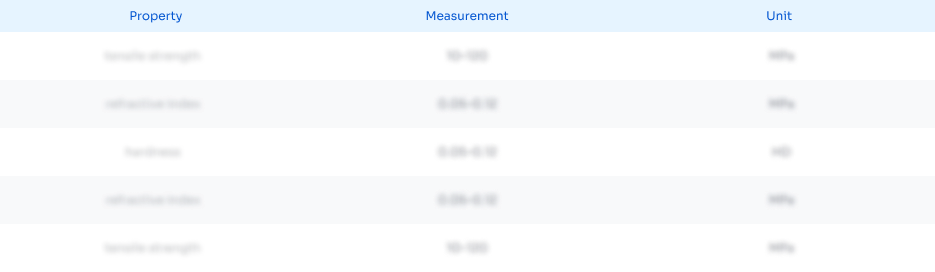
Abstract
Description
Claims
Application Information

- R&D
- Intellectual Property
- Life Sciences
- Materials
- Tech Scout
- Unparalleled Data Quality
- Higher Quality Content
- 60% Fewer Hallucinations
Browse by: Latest US Patents, China's latest patents, Technical Efficacy Thesaurus, Application Domain, Technology Topic, Popular Technical Reports.
© 2025 PatSnap. All rights reserved.Legal|Privacy policy|Modern Slavery Act Transparency Statement|Sitemap|About US| Contact US: help@patsnap.com