Automatic material-loading device of terminal crimping machine
A terminal crimping machine and automatic feeding technology, which is used in connection, circuit/collector parts, electrical components, etc. Machine production efficiency and other issues, to reduce the phenomenon of jamming or blanking errors, stable blanking, and improve the efficiency of automatic feeding
- Summary
- Abstract
- Description
- Claims
- Application Information
AI Technical Summary
Problems solved by technology
Method used
Image
Examples
Embodiment Construction
[0031] The present invention is further described in conjunction with the following examples.
[0032] The specific implementation of the automatic feeding device of a terminal crimping machine created by the present invention is as follows: figure 1 and figure 2 As shown, it includes a base 1, a turntable 2 with a cavity, a driving mechanism for driving the turntable 2 to rotate, and a material guide 6 for introducing materials into the workbench of the crimping machine. The circumferential surface is evenly provided with several blanking holes 21, the base 1 is provided with a blanking hole 11 communicating with the blanking hole 21, the material guide 6 is also fixed on the base 1, the material guide 6 is provided with a material guide groove 61, and the material guide 6 is provided with a material guide groove 61 for falling The material hole 11 communicates with the material guide groove 61 .
[0033] The upper cover of the turntable 2 is provided with a cover plate 3 ...
PUM
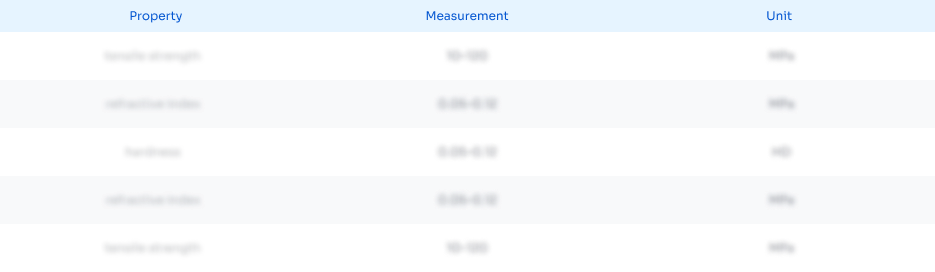
Abstract
Description
Claims
Application Information

- R&D Engineer
- R&D Manager
- IP Professional
- Industry Leading Data Capabilities
- Powerful AI technology
- Patent DNA Extraction
Browse by: Latest US Patents, China's latest patents, Technical Efficacy Thesaurus, Application Domain, Technology Topic, Popular Technical Reports.
© 2024 PatSnap. All rights reserved.Legal|Privacy policy|Modern Slavery Act Transparency Statement|Sitemap|About US| Contact US: help@patsnap.com