Bamboo-plastic strip elbow mold-pressing process and device
A bamboo-plastic and elbow technology, applied in the field of bamboo-plastic strip elbow film pressing technology and equipment, can solve the problems of high cost, expensive injection mold, low efficiency, etc.
- Summary
- Abstract
- Description
- Claims
- Application Information
AI Technical Summary
Problems solved by technology
Method used
Image
Examples
Embodiment Construction
[0019] Below in conjunction with accompanying drawing and embodiment the present invention will be further described:
[0020] See attached Figures 1 to 3 , the bamboo-plastic strip elbow membrane pressing process in the figure is characterized in that it includes the following steps:
[0021] The first step is to make a mold and carve an elbow mold with MDF;
[0022] The second step is to prepare bamboo-plastic soft strips, cut the formed bamboo-plastic straight strips into the required design size, and then put them into a heating box for heating. The heating temperature is 80-130°C, and the heating time is 12-18 minutes. Make bamboo-plastic straight strips into bamboo-plastic soft strips;
[0023] The third step is compression molding, put the bamboo-plastic soft strip described in the second step into the elbow membrane tool described in the first step, and then pressurize the elbow membrane tool through a pressurizing device, so that the bamboo-plastic soft strip The ...
PUM
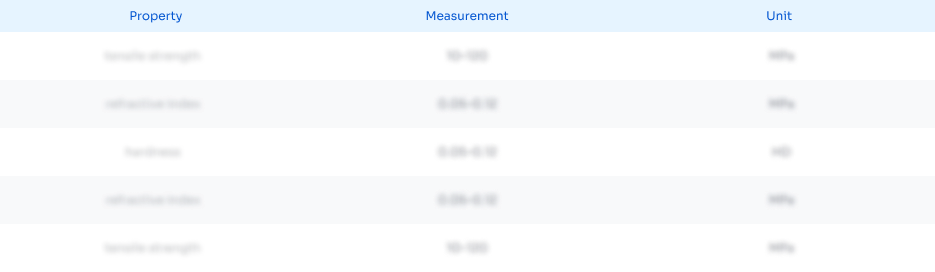
Abstract
Description
Claims
Application Information

- R&D
- Intellectual Property
- Life Sciences
- Materials
- Tech Scout
- Unparalleled Data Quality
- Higher Quality Content
- 60% Fewer Hallucinations
Browse by: Latest US Patents, China's latest patents, Technical Efficacy Thesaurus, Application Domain, Technology Topic, Popular Technical Reports.
© 2025 PatSnap. All rights reserved.Legal|Privacy policy|Modern Slavery Act Transparency Statement|Sitemap|About US| Contact US: help@patsnap.com