Oil recovery
A vegetable oil and clean technology, applied in the petroleum industry, the recovery of polluted soil, the preparation of liquid hydrocarbon mixtures, etc., can solve the problems of chemicals harmful to the environment, expensive, low-level development, etc.
- Summary
- Abstract
- Description
- Claims
- Application Information
AI Technical Summary
Problems solved by technology
Method used
Image
Examples
Embodiment 1
[0037] Concentrates were produced by blending together the following components in the indicated volume ratios (vol / vol) in a stirred reactor: 50.0% corn oil;
[0038] 25% Polyoxyethylene Sorbitan Monopalmitate (Tween Nonionic surfactant ex Croda International pic; HLB=15.6, (CAS 9005-66-7)) and
[0039] 25% Polyethylene Glycol Sorbitan Trioleate (Tween Nonionic surfactant ex Croda International pic; HLB = 11.0; (CAS 9005-70-3)).
[0040] A sample of the concentrate described above was then diluted with water (60-70° C.) in a 250 ml beaker on a stirrer hot plate to produce a cleaning solution containing 1% by volume of the concentrate. Small galvanized steel test panels were then coated with heavy fuel oil before immersion in the cleaning solution. Oil removal from the test panels was monitored by visual inspection of the beaker contents at ten minute intervals until complete removal. At this stage, the test panels were removed and washed with cold water and found to be ...
Embodiment 2
[0042] Concentrates were created by blending the following components together in the volume ratios indicated (vol / vol) in a stirred reactor:
[0043] 50.0% corn oil;
[0044] 25.0% Rewoteric AM (capryl amphopropionate surfactant; ex Evonik Industries; HLB=c.14-15) and
[0045] 25% Polyethylene Glycol Sorbitan Trioleate (Tween Nonionic surfactant ex Croda International pic; HLB = 11.0; (CAS 9005-70-3)).
[0046] A sample of the concentrate described above was then diluted with water (60-70° C.) in a 250 ml beaker on a stirrer hot plate to produce a cleaning solution containing 1% by volume of the concentrate. Small galvanized steel test panels were then coated with heavy fuel oil before immersion in the cleaning solution. Oil removal from the test panels was monitored by visual inspection of the beaker contents at ten minute intervals until complete removal. At this stage, the test panels were removed and washed with cold water and found to be free of oil. For 0.17 g o...
Embodiment 3
[0048] Another concentrate was produced by blending together the following components in the indicated volume ratios (vol / vol) in a stirred reactor: 40.0% corn oil;
[0049] 30.0% Marlowet (castor oil ethoxylate (40EO) surfactant; ex Sasol Limited; HLB=c.15-16) and
[0050] 30.0% Rewoteric AM (octyl amphetamine propionate surfactant; ex Evonik Industries; HLB=c.14-15).
[0051] A sample of this concentrate was then diluted with water (60-70° C.) in a 250 ml beaker on a stirrer hot plate to produce a cleaning solution containing 1% by volume of the concentrate. Again, small galvanized steel test panels were then coated with heavy fuel oil before dipping into the cleaning solution. Oil removal from the test panels was monitored by visual inspection of the beaker contents at ten minute intervals until complete removal. At this stage, the test panels were removed and washed with cold water and found to be free of oil. In this case, it was found that the 1% solution achieved...
PUM
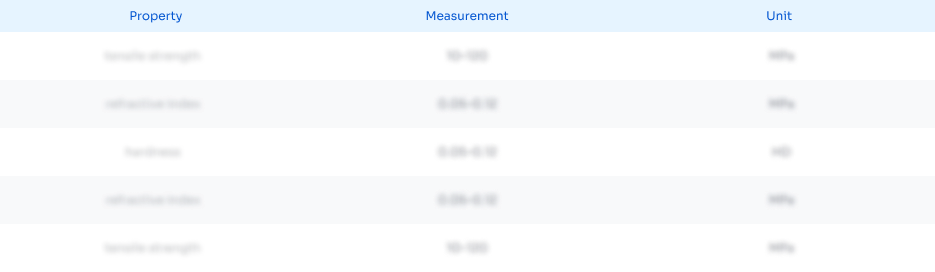
Abstract
Description
Claims
Application Information

- R&D
- Intellectual Property
- Life Sciences
- Materials
- Tech Scout
- Unparalleled Data Quality
- Higher Quality Content
- 60% Fewer Hallucinations
Browse by: Latest US Patents, China's latest patents, Technical Efficacy Thesaurus, Application Domain, Technology Topic, Popular Technical Reports.
© 2025 PatSnap. All rights reserved.Legal|Privacy policy|Modern Slavery Act Transparency Statement|Sitemap|About US| Contact US: help@patsnap.com