Aircraft seat slide rail position detection device and its measuring method
A detection device and aircraft seat technology, which is applied in the field of aircraft, can solve problems such as inaccurate installation position of slide rails, different deviations of slide rail positions, large installation position deviations, etc., and achieve the level of product quality control. The effect of less frequency and easy disassembly
- Summary
- Abstract
- Description
- Claims
- Application Information
AI Technical Summary
Problems solved by technology
Method used
Image
Examples
Embodiment Construction
[0024] Figure 1 to Figure 3 Shown is a detection device 10 for the position of an aircraft seat slide rail according to a preferred embodiment of the present invention. This detection device 10 comprises detachably fixedly installed on two parallel seat slide rails 20 ( Figure 4 and Figure 5 ) above the body 1, the body 1 is provided with at least one positioning installation part 2 on each seat slide rail and a plurality of measurement holes 3 adjacent to the positioning installation part 2, and the ball seat of the laser tracker is inserted into the measurement hole 3 in. When measuring, the laser tracker located outside the frame (such as on the ground) can measure the coordinates of the ball seat through lasers, and then obtain multiple measurement holes corresponding to the X value and Z value in the overall machine coordinate system. In the illustrated embodiment, the body 1 of the detection device 10 is configured in a triangular shape, including a positioning ins...
PUM
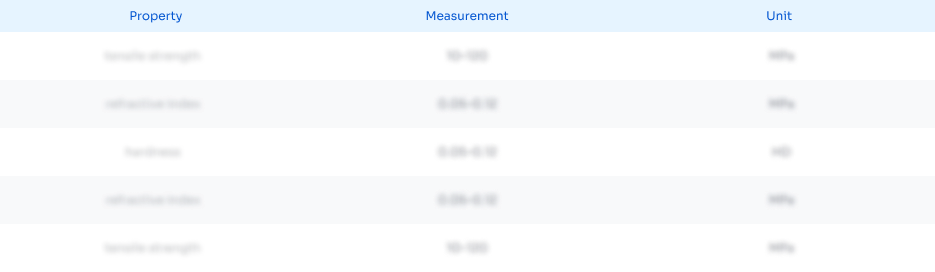
Abstract
Description
Claims
Application Information

- R&D
- Intellectual Property
- Life Sciences
- Materials
- Tech Scout
- Unparalleled Data Quality
- Higher Quality Content
- 60% Fewer Hallucinations
Browse by: Latest US Patents, China's latest patents, Technical Efficacy Thesaurus, Application Domain, Technology Topic, Popular Technical Reports.
© 2025 PatSnap. All rights reserved.Legal|Privacy policy|Modern Slavery Act Transparency Statement|Sitemap|About US| Contact US: help@patsnap.com