Stitch needle-bending tool special for wheel speed sensor
A wheel speed sensor and looper technology, which is applied in the field of wheel speed sensor special pin looper tooling, can solve the problems of not meeting the requirements of mass production, high requirements for workers' operation, and difficulty in guaranteeing bending requirements, etc., so as to reduce the scrap rate of products , Guarantee personal safety and high processing precision
- Summary
- Abstract
- Description
- Claims
- Application Information
AI Technical Summary
Problems solved by technology
Method used
Image
Examples
Embodiment 1
[0025] Example 1: Reference figure 1 . A special needle looper tooling for wheel speed sensor, including workbench 1, first looper assembly 2, second looper assembly 3, workpiece positioning head 4, first looper assembly 2, second looper assembly 3, and workpiece The positioning heads 4 are all arranged on the worktable 1, the rear side of the workpiece positioning head 4 is provided with a first looper assembly 1, and the right side thereof is provided with a second looper assembly 2. The workbench 1 is provided with two sets of touch switches 5 arranged at intervals, and the distance between the two touch switches 5 is at least 20 mm. In specific use, two hands of the worker are required to touch the touch switches 5 to start operation. The bending process is: positioning the sensor core 8 on the workpiece positioning head 4, then starting the first bending needle assembly 2 to bend the side needle 82 of the sensor inner core 8, and then starting the second bending needle ass...
Embodiment 2
[0026] Example 2: Reference figure 2 , 3 . The first looper assembly 2 includes a bending arm cylinder 21, a side needle bending arm 24, a first sliding seat 22, and a first cylinder 23. The upper end of the first sliding seat 22 is provided with a mounting cavity 221, and the upper end of the first sliding seat 22 is two An extension arm 222 extends from the lateral workpiece positioning head in the 4-direction. Both ends of the side needle bending arm 24 are connected to the extension arms 222 on both sides of the upper end of the first sliding seat 22. The cylinder end of the bending arm cylinder 21 is connected to the first sliding seat 22. The side wall or bottom wall of the mounting cavity 221 of the seat 22 is hinged, the piston rod end is eccentrically hinged to the side needle bending arm 34, the cylinder end of the first cylinder 23 is fixed to the worktable 1, and the driving end is connected to the first sliding seat 22Connect. The side needle bending arm 21 is co...
Embodiment 3
[0027] Example 3: Reference Figure 4~7 . The second looper assembly 3 includes a thimble bending roller 36, a transverse drive cylinder 34, a longitudinal drive cylinder 33, a second sliding seat 32 and a thimble stopper 37. The second sliding seat 32 is connected to the driving end of the longitudinal drive cylinder 33, A connecting frame 31 is provided on its left side. The thimble bending roller 36 is located below the connecting frame 31, and its lateral and axial ends are rotatably connected to the connecting frame 31. The cylinder end of the longitudinal drive cylinder 33 and the lateral drive cylinder 34 The drive end of the horizontal drive cylinder 34 is connected to the workbench 1. The thimble stopper 37 is horizontally arranged on the front side of the thimble bending roller 36, and the thimble stopper 37 passes through the bracket 35 and the longitudinal drive cylinder 33 The cylinder end is connected. The thimble bending roller 36 includes a roller body 364 and...
PUM
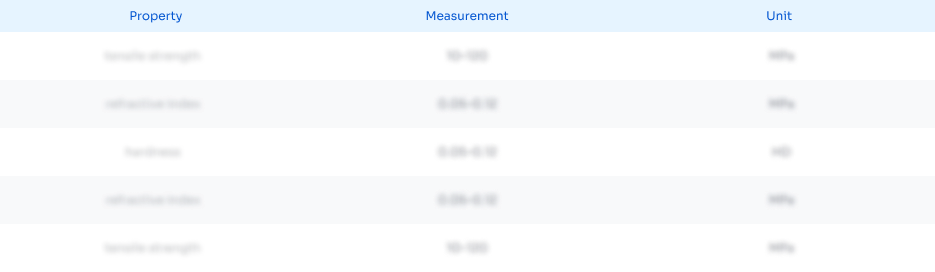
Abstract
Description
Claims
Application Information

- R&D Engineer
- R&D Manager
- IP Professional
- Industry Leading Data Capabilities
- Powerful AI technology
- Patent DNA Extraction
Browse by: Latest US Patents, China's latest patents, Technical Efficacy Thesaurus, Application Domain, Technology Topic, Popular Technical Reports.
© 2024 PatSnap. All rights reserved.Legal|Privacy policy|Modern Slavery Act Transparency Statement|Sitemap|About US| Contact US: help@patsnap.com