Impregnated Re3W-Sc2O3 mixed base cathode material and preparation method thereof
A re3w-sc2o3, cathode material technology, applied in the field of rare earth refractory metal cathode materials, can solve the problems of high working temperature, easy poisoning, and insufficient emission current of barium tungsten cathode and M-type cathode, and achieve excellent pulse electron emission performance Effect
- Summary
- Abstract
- Description
- Claims
- Application Information
AI Technical Summary
Benefits of technology
Problems solved by technology
Method used
Image
Examples
Embodiment 1
[0018] 3.6794 g Sc(NO 3 ) 3 ·6H 2 O is dissolved in analytical pure alcohol, take 60 grams of Re 3 Pour the W powder into the scandium nitrate alcohol solution, heat in a water bath and stir continuously, and after the alcohol is evaporated, take out the mixed powder and dry, grind, and sieve. The obtained powder was decomposed at 950° C. for 2 hours in a high-purity hydrogen atmosphere to obtain a precursor powder for preparing the matrix. The powder at 10t / cm 2 Pressed under the pressure of Φ3×1.5mm cathode green body, sintered under the high-purity hydrogen atmosphere, the temperature is 2000 ℃, keep warm for 30min, to obtain the cathode base material. The cathode substrate is impregnated with barium aluminate calcium salt to obtain an impregnated mixed base cathode material. After high-temperature activation treatment, test the thermal emission performance of the cathode at different temperatures, see Table 1
Embodiment 2
[0020] 3.6794 g Sc(NO 3 ) 3 ·6H 2 O is dissolved in analytical pure alcohol, take 30 grams of Re 3 Pour the W powder into the scandium nitrate alcohol solution, heat in a water bath and stir continuously, and after the alcohol is evaporated, take out the mixed powder and dry, grind, and sieve. The obtained powder was decomposed at 950° C. for 2 hours in a high-purity hydrogen atmosphere to obtain a precursor powder for preparing the matrix. The powder at 10t / cm 2 Pressed under the pressure of Φ3×1.5mm cathode green body, sintered under the high-purity hydrogen atmosphere, the temperature is 2000 ℃, keep warm for 30min, to obtain the cathode base material. The cathode substrate is impregnated with barium aluminate calcium salt to obtain an impregnated mixed base cathode material. After high-temperature activation treatment, test the thermal emission performance of the cathode at different temperatures, see Table 1
Embodiment 3
[0022] 3.6794 g Sc(NO 3 ) 3 ·6H 2 O was dissolved in analytical pure alcohol, and 14.25 g of Re 3 Pour the W powder into the scandium nitrate alcohol solution, heat in a water bath and stir continuously, and after the alcohol is evaporated, take out the mixed powder and dry, grind, and sieve. The obtained powder was decomposed at 950° C. for 2 hours in a high-purity hydrogen atmosphere to obtain a precursor powder for preparing the matrix. The powder at 10t / cm 2 Pressed under the pressure of Φ3×1.5mm cathode green body, sintered under the high-purity hydrogen atmosphere, the temperature is 2000 ℃, keep warm for 30min, to obtain the cathode base material. The cathode substrate is impregnated with barium aluminate calcium salt to obtain a new type of impregnated Re 3 W-Sc 2 o 3 Mixed base cathode materials. After the high-temperature activation treatment, test the thermal emission performance of the cathode at different temperatures, see Table 1, see figure 1
PUM
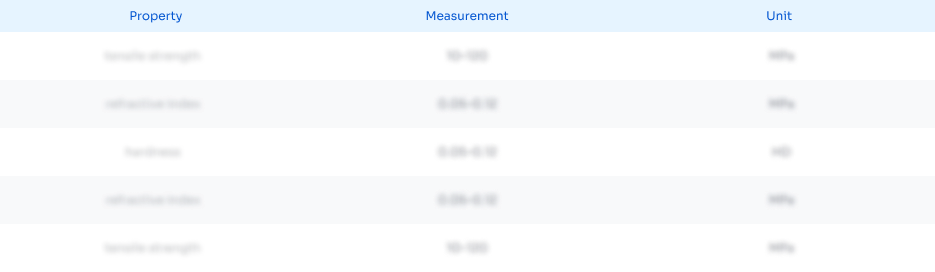
Abstract
Description
Claims
Application Information

- R&D Engineer
- R&D Manager
- IP Professional
- Industry Leading Data Capabilities
- Powerful AI technology
- Patent DNA Extraction
Browse by: Latest US Patents, China's latest patents, Technical Efficacy Thesaurus, Application Domain, Technology Topic, Popular Technical Reports.
© 2024 PatSnap. All rights reserved.Legal|Privacy policy|Modern Slavery Act Transparency Statement|Sitemap|About US| Contact US: help@patsnap.com