Power part structure of cogging mill
A blanking machine and power technology, which is applied to the structural field of the power part of the blanking machine, can solve the problems of damage to the herringbone gear set of the power reducer, inconvenient installation and connection, affecting the transmission stability, etc., to achieve a fast and smooth connection effect and improve assembly. Convenience, quick and smooth assembly
- Summary
- Abstract
- Description
- Claims
- Application Information
AI Technical Summary
Problems solved by technology
Method used
Image
Examples
specific Embodiment approach
[0022] Specific implementation methods: such as Figure 1-Figure 3 As shown, a power part structure of a blanking machine includes a power motor 1, the output end of the power motor 1 is connected to the power reducer 2 and then connected to a herringbone gear seat 3 through a coupling, and the two herringbone gear seats 3 The output end is connected to the ends of the lower roll and the upper roll through the composite joint shaft 4 and drives the lower roll and the upper roll to rotate respectively; wherein, the coupling includes a ring formed by protruding from the end of the output shaft 5 of the power reducer along the circumferential direction. A circle of flange flange 6; It also includes a connecting sleeve 8 sleeved on the end of the input shaft 7 of the herringbone gear seat. The outer ring gear 9 set on a circle of raised surface meshes, the end of the connecting sleeve 8 close to the herringbone gear seat is fixed with a screw 11 along the axial direction, and a li...
PUM
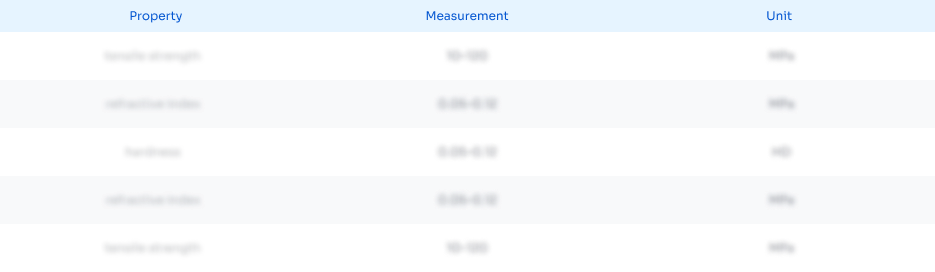
Abstract
Description
Claims
Application Information

- R&D
- Intellectual Property
- Life Sciences
- Materials
- Tech Scout
- Unparalleled Data Quality
- Higher Quality Content
- 60% Fewer Hallucinations
Browse by: Latest US Patents, China's latest patents, Technical Efficacy Thesaurus, Application Domain, Technology Topic, Popular Technical Reports.
© 2025 PatSnap. All rights reserved.Legal|Privacy policy|Modern Slavery Act Transparency Statement|Sitemap|About US| Contact US: help@patsnap.com