Integral loading cap discharge type bottle cap mould pressing forming machine
A molding machine and integral technology, which is applied to the field of integral feeding and capping cap molding machines, can solve the problems of easily breaking the scraper, affecting the rotation accuracy and increasing the production cost, etc.
- Summary
- Abstract
- Description
- Claims
- Application Information
AI Technical Summary
Problems solved by technology
Method used
Image
Examples
Embodiment Construction
[0020] The present invention relates to a bottle cap molding machine with integral material feeding and cap discharging, such as figure 1 — Figure 13As shown, it includes the host part assembly 1, the mold upper mold 2 and the mold lower mold 3 parts and the mold clamping and demoulding part 02, the oil cylinder assembly 4, the transmission mechanism 5, the slewing support 6, the feeding and discharging cover assembly 7, the outlet The material port head 8, the material outlet reversing mechanism 9 and the extrusion mechanism 10, the oil cylinder assembly 4 is driven by the hydraulic system 01, and the described loading and discharging cover assembly 7 includes a material distribution main shaft 11, on which the distribution main shaft is installed. The material tray fixing seat 12, the material distribution tray 13 is installed on the material distribution tray fixing seat, the scraper knife holder 14 is installed under the material distribution tray, the scraper knife 15 is...
PUM
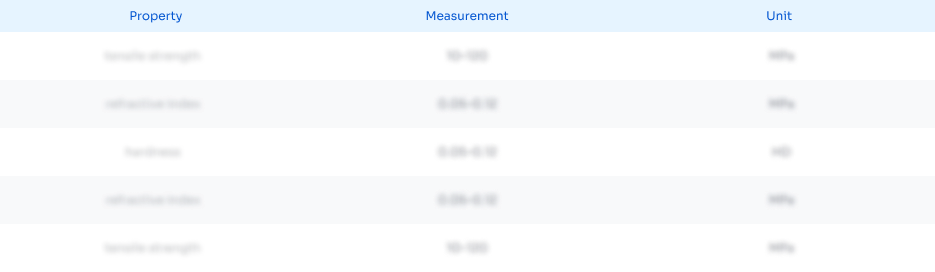
Abstract
Description
Claims
Application Information

- Generate Ideas
- Intellectual Property
- Life Sciences
- Materials
- Tech Scout
- Unparalleled Data Quality
- Higher Quality Content
- 60% Fewer Hallucinations
Browse by: Latest US Patents, China's latest patents, Technical Efficacy Thesaurus, Application Domain, Technology Topic, Popular Technical Reports.
© 2025 PatSnap. All rights reserved.Legal|Privacy policy|Modern Slavery Act Transparency Statement|Sitemap|About US| Contact US: help@patsnap.com