Thrust ball bearing ring end surface groove grinding method and device
A technology of thrust ball bearings and end faces, which is applied in the direction of abrasive surface adjustment devices, grinding workpiece supports, and parts of grinding machine tools. It can solve problems affecting machining accuracy and production efficiency, and complex grinding wheel dressing operations, so as to improve grinding wheel dressing. Accuracy, reduction of auxiliary time, and improvement of swing accuracy
- Summary
- Abstract
- Description
- Claims
- Application Information
AI Technical Summary
Problems solved by technology
Method used
Image
Examples
Embodiment Construction
[0020] Specific embodiments of the present invention will be described in detail below in conjunction with the accompanying drawings.
[0021] Such as figure 1 As shown, in the method of the present invention, the ferrule of the thrust ball bearing is clamped by the clamping mechanism on the workpiece spindle 18 with the center line in a transverse state, and the forming disc type grinding wheel 2 with the outer circular surface as the arc surface is used as the grinding tool , the ferrule 1 rotates with its own center line as the center of rotation, the center line of the grinding wheel 2 is perpendicular to the center line of the ferrule 1, the grinding wheel 2 rotates at a high speed and its arc outer surface is tangent to the groove of the end face of the ferrule In contact, the trimming pen 3 for circular arc swinging motion is arranged in front of the workpiece spindle 18 to trim the shape of the grinding wheel 2. On one plane, the grinding wheel 2 only moves in a strai...
PUM
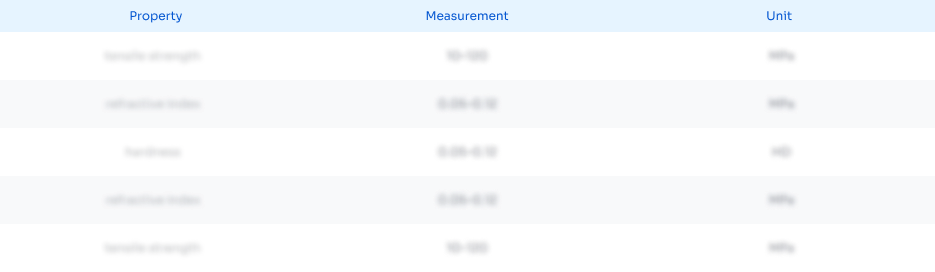
Abstract
Description
Claims
Application Information

- R&D Engineer
- R&D Manager
- IP Professional
- Industry Leading Data Capabilities
- Powerful AI technology
- Patent DNA Extraction
Browse by: Latest US Patents, China's latest patents, Technical Efficacy Thesaurus, Application Domain, Technology Topic, Popular Technical Reports.
© 2024 PatSnap. All rights reserved.Legal|Privacy policy|Modern Slavery Act Transparency Statement|Sitemap|About US| Contact US: help@patsnap.com